Mastering Odoo Inventory Management for Businesses
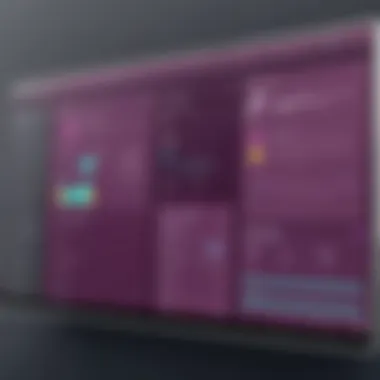
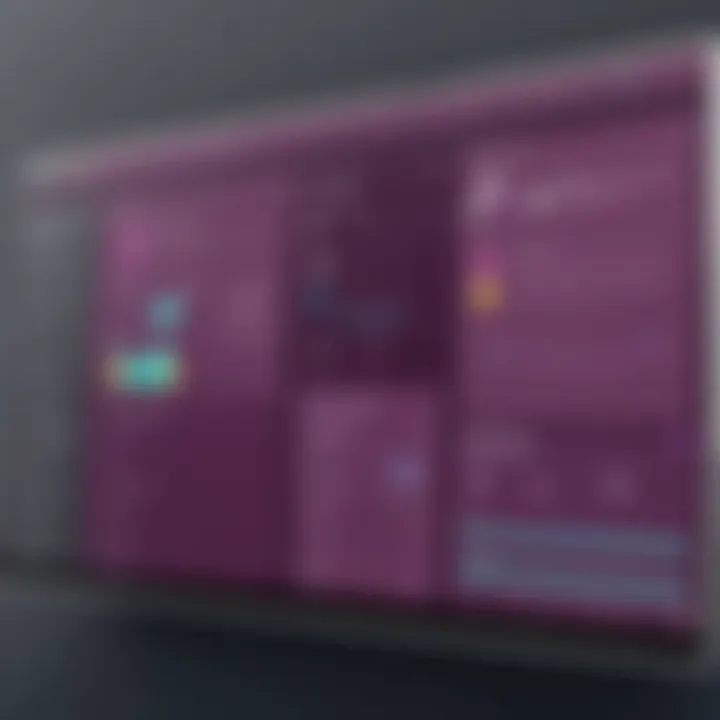
Intro
Inventory management has evolved into a cornerstone of successful business operations. The introduction of sophisticated software solutions like Odoo has transformed the way organizations oversee their stock. Odoo's inventory management module offers an array of features tailored for businesses of all sizes, supporting the efficient handling of stock, tracking order fulfillment, and ultimately reducing costs.
Understanding the inner workings of Odoo's inventory capabilities can provide a competitive edge. In this guide, we aim to dissect the various components that make up Odoo Inventory Management, revealing best practices, key features, and implementation strategies that can enhance operational efficiency. We're diving deep into an analytical overview, providing insights that will arm tech-savvy professionals and business owners with the knowledge to make well-informed decisions.
Let’s embark on this journey to unravel the functionalities of Odoo and how they can align with your inventory needs.
Software Needs Assessment
Before diving into the specifics of Odoo, it's crucial to evaluate your software needs. A meticulous assessment of user requirements paves the ground for selecting and implementing the right features tailored to your operations.
Identifying User Requirements
Understanding the unique needs of your team is the initial step in this evaluation. Here are some considerations:
- Team Size and Structure: Who will be using the software? Sales teams, warehouse staff, and management typically have different needs.
- Inventory Complexity: Are you managing a single warehouse or multiple locations? Do you handle numerous product variations?
- Integration Needs: Does the software need to communicate with other tools such as accounting or sales platforms?
An effective way to identify these requirements is through discussions with key stakeholders. Garner feedback from your teams about their daily challenges and what they hope to achieve through improved software.
Evaluating Current Software Solutions
After pinpointing your user needs, it’s time to assess existing software solutions:
- Performance: How well does your current setup meet your business demands?
- User Experience: Are your team members comfortable with the existing software? Are there frequent complaints about usability?
- Cost: Is the ROI justifiable? Are there hidden costs associated with maintenance and training?
Performing a SWOT analysis (Strengths, Weaknesses, Opportunities, Threats) of your current system can provide valuable insights and steer you towards Odoo's capabilities that might fill any gaps.
Data-Driven Insights
In an era where data reigns supreme, leveraging market trends and performance metrics becomes indispensable. Odoo's inventory management is imbued with features that harness data to optimize your inventory processes.
Market Trends Overview
The landscape of inventory management is continually shifting. Notable trends to keep an eye on include:
- Automation: The increasing throughput of automation tools.
- AI and Predictive Analytics: Utilizing data from various sources to predict inventory needs.
- Sustainability: Emphasizing eco-friendly practices in inventory management.
Staying ahead of these trends ensures your inventory processes remain relevant and competitive.
Performance Metrics
Several key performance indicators (KPIs) can illuminate the efficiency of your inventory management, such as:
- Inventory Turnover Ratio: This metric reflects how quickly inventory is sold and replaced over a given period.
- Order Fulfillment Time: Measuring the speed at which orders are completed.
- Stock Out Rate: Tracking how often you run out of stock can inform purchasing decisions.
Analyzing these KPIs within Odoo can guide strategic decisions, helping to optimize your inventory for both cost efficiency and responsiveness.
"The strength of your inventory management system directly impacts your overall business performance."
By understanding your software needs, assessing current operations, and leveraging data insights, you create a solid foundation for successfully utilizing Odoo Inventory Management.
Prolusion to Odoo Inventory Management
In the realm of business, managing inventory sits at the core of operational efficiency. Odoo Inventory Management has emerged as a robust tool tailored for various business needs, simplifying tasks that can often drain resources and sap productivity. The significance of mastering inventory management cannot be overstated, as it encompasses more than just keeping count of stock; it involves strategic control over every asset from the moment it enters a warehouse to its eventual sale or utilization.
Navigating through fluctuating market demands while minimizing costs requires an adept handling of inventory. Through careful management, organizations can ensure that they always have the right products on hand, ultimately paving the way for enhanced customer satisfaction and improved profit margins. This article unpacks the nuances of Odoo’s capabilities, breaking it down into manageable segments that guide readers toward understanding how to leverage this software for maximum impact.
Understanding the Importance of Inventory Management
Inventory management plays a critical role in determining an organization’s success. Without a solid understanding of quantities in stock, businesses can easily find themselves at a disadvantage. Imagine running a bakery that has no idea how much flour or sugar is on hand—it would only take a couple of busy days to run out of key ingredients, leading to lost sales and unhappy customers.
Effective inventory management involves various strategies and technologies that work in concert to:
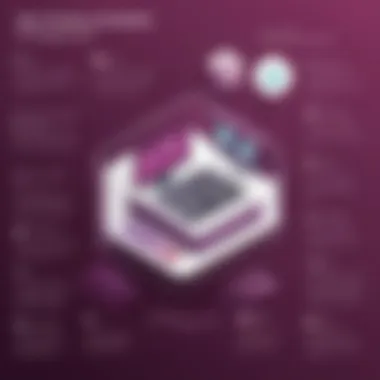
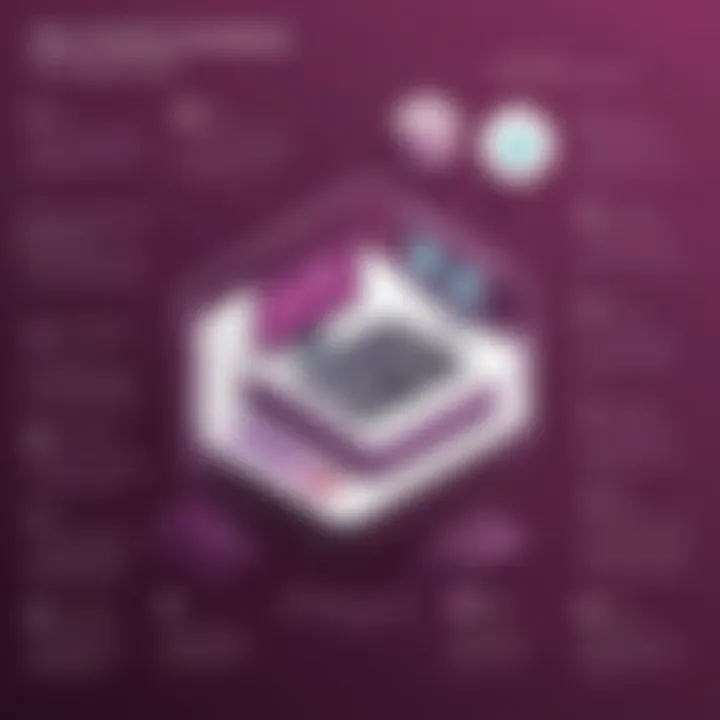
- Minimize excess stock: Carrying surplus stock can tie up capital that could be better utilized elsewhere.
- Prevent stockouts: Running out of a popular item can lead to missed sales opportunities and a tarnished reputation.
- Enhance operational efficiency: By optimizing the flow of inventory, resources can be allocated more effectively, impacting the bottom line positively.
This is precisely where Odoo Inventory Management comes in. It offers a comprehensive approach that helps businesses not just to view their stock levels but also to analyze trends, forecast needs, and streamline processes that contribute to operational success.
Overview of Odoo as a Business Solution
Odoo is not merely an inventory management system; it's a complete suite of applications that serve various facets of business management. From manufacturing to sales, finance to project management, Odoo provides an integrated ecosystem where every module can communicate and share information seamlessly.
- User-friendly interface: Odoo has designed a platform that is both intuitive and powerful. Businesses can easily navigate the platform, ensuring that even those with minimal tech experience can operate it effectively.
- Scalability: Odoo grows with your business. Whether you’re a freshly minted startup or a seasoned enterprise, Odoo can expand its offerings tailored to your specific needs.
- Community-driven development: With an active community, Odoo is continually being enhanced. As users provide feedback and new features are rolled out, the system remains on the cutting edge.
This comprehensive approach allows businesses to manage inventory alongside other critical operations, making Odoo a compelling choice for those looking to navigate the complexities of today's market more effectively.
"Managing inventory does not just involve counting items; it’s about understanding your business's lifeblood and ensuring its continuous flow."
In essence, Odoo Inventory Management empowers businesses to refine their inventory processes that can help save time, cut costs, and enhance overall efficiency. Through this article, we will explore these features further, providing an insightful guide that equips you to make informed decisions tailored to your unique circumstances.
Core Features of Odoo Inventory Management
The realm of inventory management is where efficiency meets organization, and Odoo's inventory module stands tall with an array of core features designed to streamline processes. When we speak of Odoo's inventory management, we’re not merely discussing a software tool; we’re delving into a comprehensive solution that reshapes how businesses manage their stock. These features not only enhance accuracy but also greatly influence productivity across different business sizes.
Real-time Inventory Tracking
Real-time inventory tracking is a game changer. With Odoo, you no longer have to wait for periodic updates or rely on manual stock counts. Imagine being able to glance at a dashboard and see exactly what’s on your shelves. This feature allows businesses to maintain accurate stock levels, thereby reducing the chances of stockouts or overstocking.
Here's why this matters:
- Transparency: Stakeholders can view stock levels instantly, promoting trust and accountability.
- Informed Decisions: Managers can make faster, data-driven decisions based on current stock status.
- Reduced Waste: With accurate data, chances of obsolescence and wastage decrease significantly.
"Information is power; with real-time data, businesses can empower themselves to be proactive rather than reactive."
Multi-warehouse Operations
In today's global economy, multi-warehouse operations are not a luxury; they are a necessity. Odoo provides the ability to manage several warehouses seamlessly. This is crucial for businesses operating in multiple locations or serving various markets. With this functionality:
- Centralized Management: Admins can oversee all warehouses from one interface. Simplified control saves time and reduces errors.
- Localized Strategies: Different warehouses can have tailored stock levels and management strategies that align with local demand.
- Efficient Dispatch: Orders can be routed from the nearest warehouse automatically, minimizing shipping costs and time.
Automated Reordering Rules
As the saying goes, "An ounce of prevention is worth a pound of cure," and Odoo embodies this philosophy with its automated reordering rules. This feature allows users to set thresholds for inventory levels, triggering automatic purchase orders to suppliers when stocks run low.
- Time-saving: This automation removes the need for constant manual monitoring.
- Efficiency: Companies can focus on core operations instead of worrying about stock levels.
- Cost-effective: Keeping inventory at optimal levels leads to better cash flow management.
Barcode Scanning Integration
The integration of barcode scanning in Odoo takes accuracy to another level. Using barcodes, companies can track inventory movement quickly and accurately. It diminishes the occurrence of human error associated with manual entry. Key benefits include:
- Speed: Scanning barcodes is faster than typing, allowing staff to handle larger volumes without compromising accuracy.
- Control: Easily keep track of stock checks, receipts, and shipments.
- User-friendly: Even team members with little technical knowledge can use this system with minimal training.
Overall, these core features empower businesses to optimize their inventory management tasks effectively. By embracing these tools, companies can not only increase operational efficiency but also enhance customer satisfaction through improved service levels.
Integrating Odoo Inventory with Other Odoo Modules
Integrating Odoo Inventory with other modules within the Odoo ecosystem creates a seamless flow of data and processes that can significantly enhance operational efficiency. This interconnectivity taps into the power of integrated business management, ensuring that you’re not just moving inventory but managing it holistically. The benefits of such integrations extend beyond mere convenience; they lead to informed decision-making, improved customer satisfaction, and ultimately, increased profitability.
Linking Inventory with Sales Management
When you connect inventory with sales management, you pave the way for real-time visibility into stock levels directly from the sales interface. This means sales personnel can instantly view what is available for sale without having to check multiple systems. Imagine a scenario where a sales rep can see live inventory count while talking to a customer about a new product—this nimbleness can clinch sales that might otherwise slip through the cracks.
Benefits of this integration include:
- Improved Accuracy: Reduces chances of overselling products that aren’t in stock.
- Streamlined Order Processing: Automatically updates inventory when sales are made, keeping stock levels accurate.
- Enhanced Customer Satisfaction: Customers get timely information about product availability, which fosters trust and loyalty.
Integration with Procurement Processes
Integrating inventory management with procurement processes allows businesses to synchronize demand forecasting with inventory levels efficiently. When procurement is aware of current stock levels and upcoming sales orders, it can place orders more strategically, ensuring that the business remains well-stocked without over-purchasing.
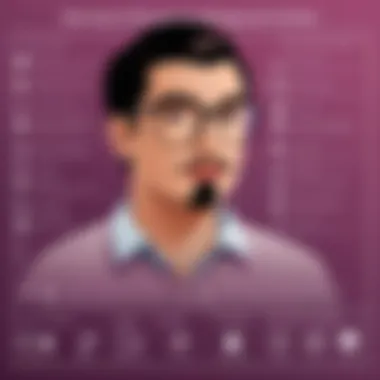
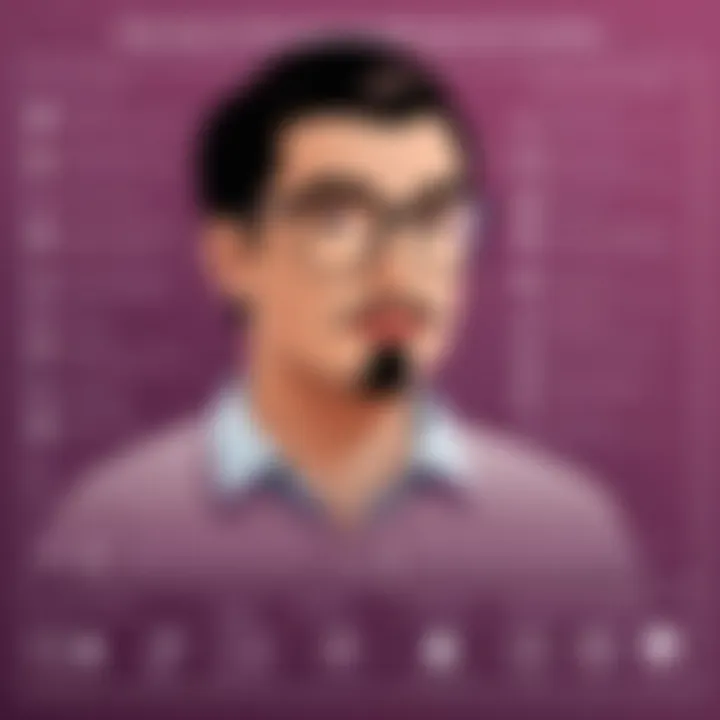
Considerations for this integration include:
- Demand Planning: Use sales data to predict future inventory needs, leading to better supplier relations and terms.
- Supplier Performance Tracking: Track how well suppliers meet deadlines and quantity requirements, which can help fine-tune procurement processes.
- Cost Efficiency: Reduces storage costs and waste, making the operation leaner and more responsive to market demands.
Enhancements through Manufacturing Module
For businesses involved in manufacturing, integrating inventory management with the manufacturing module is nothing short of essential. This integration provides manufacturers with the visibility they need to efficiently manage raw materials, production processes, and finished goods.
Important points to consider include:
- Real-time Tracking: Know exactly how much raw material is available and how much is needed for upcoming production runs.
- Production Efficiency: Automatically update inventory based on production output; if a product is created, it gets added to inventory without manual intervention.
- Inventory Cost Control: Helps maintain optimal levels of raw materials, preventing excess that can tie up cash flow.
“The art of workflow in a business does not just lie in individual departments but in how they come together. Odoo shines when modules communicate.”
Merging inventory with other Odoo modules makes it easier to cultivate a dynamic business environment. This means quicker adaptations to changing markets and a cohesive strategy that boosts overall performance. When sales, procurement, and manufacturing work hand-in-hand within Odoo, it minimizes friction, maximizes productivity, and optimizes every aspect of inventory handling.
Implementing Odoo Inventory Management in Your Business
Implementing Odoo Inventory Management is not just a technical step but a strategic move that can enhance your business operations considerably. It allows companies to streamline their inventory processes, thereby achieving improved efficiency, reducing costs, and ultimately driving profits. Every organization, whether small or large, grapples with inventory management challenges. Without a robust system in place, stockouts, overstock, and misplaced items can mean lost revenue. Therefore, investing the time to set up Odoo's inventory management is essential to curtail these issues and boost overall productivity.
Preparing for Implementation
Before leaping into the implementation of Odoo Inventory Management, businesses must lay a solid foundation. This means analyzing current inventory practices, identifying areas where automation and optimization are needed, and setting clear goals for implementation.
- Assess Current System: Evaluate existing inventory management methods. Understand what works and what doesn't, which can serve as a checkpoint in tailoring Odoo to specific needs.
- Set Clear Objectives: Define what you hope to achieve with the new system. Are you aiming for greater accuracy, improved speed in processing orders, or better integration with other business functions? These objectives will guide your implementation strategy.
- Gather Your Team: Involve pertinent team members in discussions to assess needs and expectations. Getting input from those directly involved in inventory tasks can highlight essential features that should not be overlooked.
Data Migration Strategies
Transitioning to Odoo requires careful consideration, especially when it comes to data migration. Poor migration can lead to data corruption or loss, which can create a ripple effect down the line. Here are some strategies to consider:
- Cleanse Your Data: Before moving data, conduct a thorough audit. Remove any duplicates, inconsistencies, or outdated entries.
- Use Import Tools: Utilize Odoo’s built-in import tools to streamline the data transfer process. This often helps to reduce errors significantly.
- Test Migrations: Conduct trial migrations to identify potential issues without risking your actual data. Run thorough tests and correct any discrepancies
- Backup Everything: Always back up current inventory records in a secure location. Should something go wrong, having a backup ensures that vital records remain safe.
Training Employees and Users
Once Odoo Inventory Management is implemented and data is successfully migrated, the next step revolves around training employees and users effectively.
- Tailored Training Sessions: Offer sessions that focus on specific functionalities relevant to different teams. For example, finance staff may need to know about inventory valuation while the warehouse team may require hands-on operational training.
- Use Odoo’s Resources: Leverage Odoo’s official documentation and community forums. They provide valuable insights and troubleshooting resources that can help employees adapt more swiftly.
- Feedback Loop: Encourage employees to share their experiences and challenges. This feedback can be advantageous for refining training efforts and ensuring a smoother transition.
"Investing in training is as crucial as investing in the software itself; both create a solid groundwork for success."
Investing time and resources into effectively implementing Odoo Inventory Management is not merely a box to tick but a strategic step towards an organized, efficient, and profitable future. By preparing adequately, migrating data correctly, and ensuring employees are well-trained, businesses can truly harness the full potential of Odoo.
User Experiences and Case Studies
In discussing Odoo Inventory Management, examining real-life user experiences and case studies plays a crucial role. These accounts offer insights into the system's practicality and effectiveness in various business settings. They serve as a testament to how Odoo can shape inventory management practices and highlight both success stories and challenges faced by different organizations.
Incorporating user experiences not only enriches the information presented but also lends a relatable facet to the technical details. Seeing how a local bakery improved its order accuracy or a large manufacturing company streamlined its inventory processes can demonstrate the tangible benefits of Odoo's inventory features. Moreover, these stories help prospective users envision how they could leverage the software to solve their unique challenges.
Understanding the diverse range of implementations—small businesses vs. large enterprises—provides a comprehensive view of the adaptability and scalability of Odoo. This understanding is essential in making informed decisions about whether to adopt the system.
Case Study: Small Business Success
Consider the case of a small retail business named "Crafted Creations," which specializes in handmade home decor. Before adopting Odoo, they relied on a spreadsheet for tracking inventory, leading to frequent stockouts and overordering.
After integrating Odoo Inventory Management, Crafted Creations experienced a significant turnaround. The real-time inventory tracking feature allowed them to keep an accurate pulse on stock levels. This was particularly beneficial during peak seasons, such as the holidays, when demand surged unexpectedly. By setting automated reordering rules, the owner managed to reduce excess inventory by 30%, freeing up capital that could be reinvested into marketing and product expansion.
Furthermore, bar scanning integration enabled the team to speed up checkout processes, enhancing customer satisfaction. Post-implementation surveys revealed that 90% of customers noted improvements in service speed, while the business reported a revenue increase of over 15% in the first quarter alone.
Case Study: Enterprise-Level Implementation
On the other end of the spectrum lies "Global Tech Industries," a massive player in the electronics sector. With multiple warehouses and diverse product lines, managing inventory was a daunting task. Prior to Odoo, scattered systems caused serious delays in inventory audits and order fulfillment, resulting in significant lost sales.
Upon implementation of Odoo Inventory Management, the company saw a complete overhaul of their warehousing procedures. The multi-warehouse functionality allowed them to track inventory across locations seamlessly. By integrating inventory with sales management, they could quickly assess stock availability before processing customer orders.
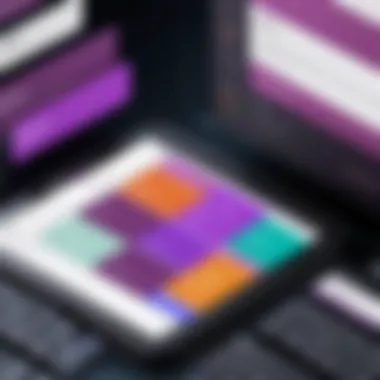
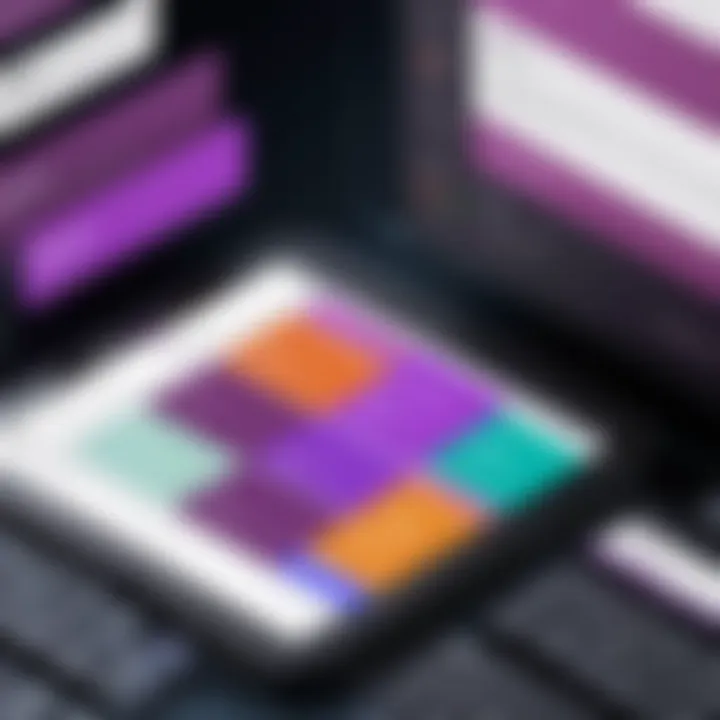
Additionally, the predictive analytics tools in Odoo helped Global Tech optimize stock levels based on past sales trends. Implementing this level of automation not only reduced manual errors but also improved service levels, leading to a customer satisfaction rating of 95% in the following year. This comprehensive approach to inventory helped return over $1 million to the bottom line due to improved efficiency and reduced waste.
Both of these case studies serve as a powerful reminder that Odoo Inventory Management is not just software; it's a tool for transformation, scalable from small businesses to large enterprises. They shed light on how appropriate implementation can lead to measured growth, enhanced customer experiences, and ultimately lead to sustained business success.
Potential Challenges and Solutions
The realm of inventory management is fraught with potential bumps on the road, particularly when businesses decide to embrace software like Odoo. Understanding and addressing these challenges is integral to ensuring a seamless integration and operational success. This section focuses on common pitfalls faced during implementation and highlights the importance of fostering user engagement to minimize resistance to change.
Common Implementation Pitfalls
Implementing Odoo for inventory management can resemble navigating a maze—plenty of twists and turns, and occasionally running into walls. Let’s take a look at frequent snags companies hit during this process:
- Lack of Clear Objectives: Many firms dive headfirst into implementation without setting precise goals. This can lead to misguided efforts and insufficient outcomes. It’s crucial to outline what success looks like for inventory management ahead of time.
- Insufficient Training: Throwing new software at users without proper training is like giving someone a map of a city they've never visited, then expecting them to navigate flawlessly. To start, training should be tailored to different user levels, from novices to seasoned pros.
- Data Migration Issues: Moving existing inventory data over to Odoo can present challenges such as data loss or corruption. Without a solid strategy, this migration could become a nightmare, leading to inaccurate inventory records.
- Resistance to Change: People are often hesitant to adapt to new systems. This reluctance can create bottlenecks and slow down the whole process. Addressing the human element of change management is vital for success.
Every one of these pitfalls can set back even the best-laid plans. Therefore, tackling them head-on is essential to leverage the full capabilities of Odoo Inventory Management.
Addressing User Resistance
Resistance among users is a common hurdle when introducing new systems. The feelings of uncertainty or disruption can interfere with how effectively a team utilizes Odoo. Here are ways to tackle this issue:
- Involve Users Early: Getting input from the end-users during the planning stage can pave the way for smoother acceptance. When employees feel heard, they are more likely to support the change.
- Communicate the Benefits: It helps to emphasize how the change will enhance their day-to-day tasks. Showing how Odoo can save time or reduce errors can turn skeptics into advocates.
- Offer Ongoing Support: Establishing a robust support system post-implementation is crucial. If users know they can reach out for help, they are more inclined to embrace the new system fully.
"Change is hard at first, messy in the middle, and gorgeous at the end." – Robin Sharma. Remember, the journey toward successful inventory management with Odoo may have its hurdles, but the rewards often outweigh the initial pain.
By focusing on these strategies, businesses can smooth over the bumps that often accompany the switch to more sophisticated inventory management tools like Odoo. Addressing challenges thoughtfully and preparing users for transitions means surfacing potential problems before they can take root. Through this proactive approach, companies can better harness Odoo’s power and drive operational efficiency.
Future Trends in Inventory Management Software
Staying ahead in the fast-paced business world involves understanding where technology is headed. In this day and age, when efficiency and accuracy are the name of the game, the future of inventory management software is not just important; it’s crucial. Businesses of all sizes are increasingly relying on these technologies for better inventory oversight, cost control, and overall operational excellence. Let’s have a closer look at what’s trending in the realm of inventory management software, particularly through the lens of Odoo.
Emerging Technologies in Inventory Management
The landscape of inventory management is being reshaped by several groundbreaking technologies. Among these, Internet of Things (IoT) and blockchain are at the forefront.
- Internet of Things (IoT): Businesses are utilizing IoT devices to gain real-time data on their inventory levels. Sensors can track the movement of products from the warehouse to the customer, reducing errors and optimizing stock levels. This leads to enhanced decision-making.
- Blockchain: This can turn inventory tracking into a secure, streamlined process. By providing an immutable ledger, it helps in preventing fraud and enhances transparency across supply chains.
- Augmented Reality (AR): Imagine using AR glasses to navigate a warehouse, instantly accessing inventory data just by looking at a product. This technology could make training more efficient and improve picking operations.
With these technologies emerging, businesses won't just be reacting to inventory issues but proactively addressing them long before they become problems. The bottom line? Adapting to these technologies can lead to tangible cost savings and more efficient operations.
The Role of AI in Automated Inventory Management
Artificial intelligence is becoming the brain behind effective inventory management systems. By analyzing historical data, AI can forecast demand with incredible accuracy. This means that businesses can avoid the pitfalls of overstocking and stockouts, which can be costly.
For instance, advanced algorithms can analyze various data points:
- Sales trends: Understanding which products fly off the shelves during specific seasons can help in planning.
- Market conditions: Changes in the economy, such as a recession or growth period, influence consumer behavior.
- Supply chain disruptions: AI can detect patterns that indicate potential disruptions, allowing managers to make data-driven adjustments.
By leveraging AI, companies can set reorder levels that dynamically adjust based on predictive analytics, ensuring inventory aligns with actual market demand. Moreover, this kind of automation reduces the workload on staff, allowing them to focus on strategic tasks rather than mundane inventory checks.
"Ignoring future trends in inventory management software is like sailing a ship without a compass—you're bound to drift off course."
Epilogue and Recommendations
In the fast-paced world of business, the importance of effective inventory management cannot be overstated. The Odoo Inventory Management module stands as a robust solution designed to simplify complex inventory challenges. By having an organized inventory management system, businesses can streamline their operations, minimize costs, and enhance overall efficiency. The critical takeaway is that an efficient inventory process is not just a nice-to-have; it's a fundamental aspect that can steer business growth and customer satisfaction.
Summarizing Key Takeaways
The essence of this article has been to dissect the various dimensions of Odoo Inventory Management and its practical implications. Here are the key points to keep in mind:
- Real-time Tracking: Knowledge about inventory levels in real-time can make or break a business's responsiveness.
- Integration Capabilities: Linking inventory management with other Odoo modules creates a seamless flow of information, reducing the risk of errors while enhancing productivity.
- User Experience Matters: Case studies illustrate that proper implementation leads to happier employees and more satisfied customers.
- Future Proofing: Staying ahead of technology trends helps businesses adapt and thrive; Odoo continues to evolve to incorporate emerging technologies.
This knowledge presents clarity on why investing in a competent inventory management system is vital for both small and large businesses alike.
Final Recommendations for Implementation
When considering implementation of Odoo Inventory Management, several recommendations can facilitate a smoother transition and effective use:
- Thorough Needs Assessment: Before diving into implementation, assess your business needs to ensure the software aligns with your operational demands.
- Data Migration Planning: Carefully plan the data transfer from your old system to Odoo. Inconsistent or lost data can have ripple effects on other processes.
- Training is Key: Invest time in training the team. A system is only as good as its users; knowledgeable employees will leverage the software effectively.
- Customizable Workflows: Leverage Odoo's flexibility by customizing workflows that fit your unique business model. Don’t shy away from modifying templates.
- Ongoing Support and Evaluation: Establish a support system for troubleshooting and continuous improvement. Regularly evaluate inventory processes to capture insights that can lead to further refinements.
"An efficient inventory system is the backbone of a thriving business."
The landscape of inventory management is shifting, and being proactive will always yield worthwhile dividends.