Comprehensive Inventory Management Solutions for Food
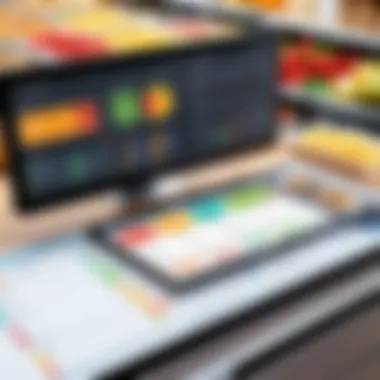
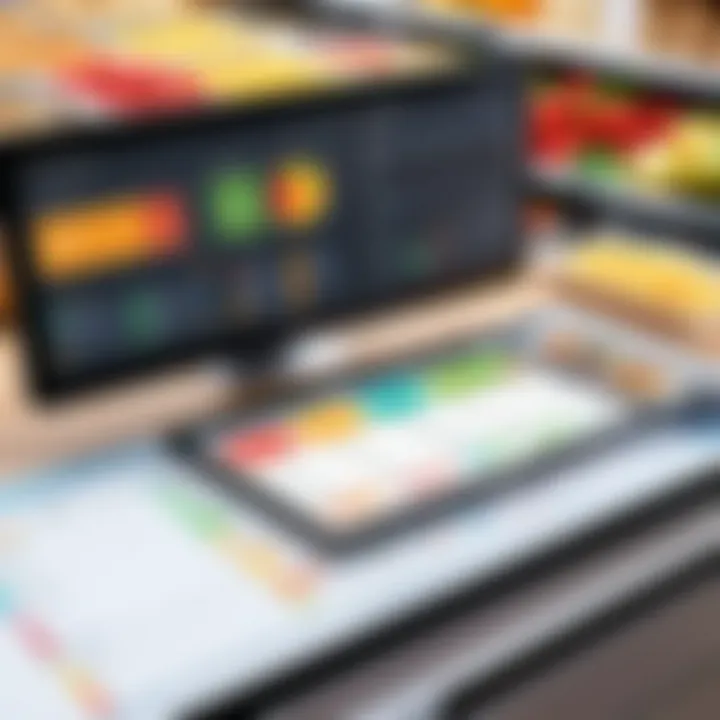
Intro
Inventory management systems are vital for the food industry. They play a critical role in maintaining product quality and ensuring compliance with health regulations. These systems help businesses track their inventory efficiently, preventing overstocking or stockouts.
Yet, many in the food sector still struggle with traditional methods. Paper records or basic spreadsheets often lead to errors. These inaccuracies can have severe consequences in food safety and business operations.
Thus, there is a pressing need for sophisticated inventory management solutions tailored specifically for the nuances of the food industry. They provide real-time data and insights, facilitating better decision-making.
The following sections will discuss important aspects of inventory management systems, including software needs assessment, data-driven insights, and various challenges that businesses face. We aim to equip decision-makers in the food industry with knowledge that leads to effective implementation of these systems.
Software Needs Assessment
When considering an inventory management system, a software needs assessment is crucial. It lays the groundwork for a successful integration of technology into existing business processes.
Identifying User Requirements
Each business in the food industry has unique requirements. Identifying these needs is the first step in choosing the right system. Involve various stakeholders such as warehouse staff, sales teams, and management. Understanding their daily challenges ensures the chosen software aligns with operational goals.
Key aspects to consider are:
- Types of Products: Perishable goods require different handling compared to non-perishables.
- Volume of Inventory: High turnover rates may necessitate more robust tracking features.
- Operational Processes: Requirements may vary based on whether the business is a restaurant, distributor, or manufacturer.
Evaluating Current Software Solutions
The next step involves evaluating existing software solutions. Understanding the features of various inventory management systems helps in narrowing choices. Important factors to consider include:
- Scalability: Will the software adapt as the business grows?
- Integration Capabilities: How well will it work with current systems such as accounting or point-of-sale?
- User Interface: An intuitive design increases user adoption and minimizes training time.
Gather feedback from user reviews and expert opinions to assess the effectiveness of different systems.
Data-Driven Insights
In today’s data-centric world, businesses must utilize data-driven insights to remain competitive. Evaluating market trends and performance metrics helps businesses understand their position and optimize inventory management.
Market Trends Overview
The food industry often faces rapidly changing trends. Recent shifts have shown increased consumer demand for transparency in sourcing and sustainability. Companies need to adapt by managing inventory according to these customer preferences. Furthermore, automation in inventory processes is rising, with many adopting AI technologies to predict demand more accurately.
Performance Metrics
Key performance metrics provide vital insights into operational efficiency. Monitoring these metrics helps in optimizing inventory levels:
- Turnover Rate: Indicates how quickly inventory is sold.
- Shrinkage Rate: Measures losses due to damages or theft.
- Stockout Frequency: Tracks how often items are unavailable, which can affect customer satisfaction.
By continuously analyzing these metrics, businesses can refine their inventory strategies, ensuring they meet market demands effectively.
"Data-driven strategies lead to improved decision-making in inventory management."
Preamble to Inventory Management Systems
Managing inventory is a critical element in any business, but it takes on heightened significance in the food industry. Inventory management systems assist in the tracking of stock levels, managing orders, and minimizing waste. This section focuses on the definition, purpose, and importance of these systems, seeking to explain their relevance in an industry that is often characterized by rapid turnover and strict regulations.
Definition and Purpose
An inventory management system is a technology solution designed to oversee the flow of products, from procurement and storage to sales and delivery. The primary purpose of such a system is to ensure that businesses maintain adequate stock levels without overstocking or running out, which can lead to lost sales and unhappy customers. In the food sector, where products can perish quickly, efficient management is even more essential. Systems can automate reordering processes, provide real-time stock updates, and assist in demand forecasting. This functionality streamlines operations and ultimately saves time and costs.
Importance in the Food Industry
The food industry faces unique challenges that make effective inventory management vital. According to the U.S. Department of Agriculture, about 30 to 40 percent of the food supply is wasted. An effective inventory system can reduce this waste significantly.
- Perishability: Food products spoil quickly. Without an efficient system, businesses risk losing entire batches to spoilage.
- Regulatory Compliance: The food sector is heavily regulated. Non-compliance can lead to hefty fines and loss of reputation. An inventory system helps track key data needed for compliance.
- Consumer Demand: Fluctuations in consumer preferences can affect supply. Inventory systems allow businesses to adapt quickly to market changes, ensuring the right products are available at all times.
Key Challenges in Food Inventory Management
Effective inventory management in the food industry is crucial due to its complexity and unique challenges. The industry faces various hurdles that can significantly affect its efficiency, profitability, and compliance with regulations. Understanding these challenges allows businesses to tailor their inventory strategies to meet operational demands. This section examines three prominent challenges: perishability of goods, seasonal demand fluctuations, and regulatory compliance issues.
Perishability of Goods
The perishability of food items is a primary concern for businesses. Unlike conventional products, many food items have limited shelf lives, which necessitates precise tracking and management. If perishables are not sold in time, they become waste, leading to significant losses. To address this challenge, companies must implement robust inventory systems that facilitate real-time tracking of stock levels and expiration dates. Utilizing technologies such as barcode scanning or RFID can help enhance monitoring and reduce spoilage.
Moreover, incorporating a first-in, first-out (FIFO) method in inventory management is essential. This practice ensures that older stock is sold first, minimizing the risk of selling expired products. Effective forecasting also plays a role; businesses need to anticipate demand accurately to avoid overstocking commodities that could perish before sale.
Seasonal Demand Fluctuations
Seasonal demand fluctuations present another significant challenge in food inventory management. During specific times of the year, such as holidays or local festivals, demand for certain products can peak unexpectedly. Conversely, off-seasons can lead to excess inventory that ties up valuable resources. To manage these fluctuations, businesses should develop flexible inventory strategies that can adapt to changing market conditions.
Employing historical sales data from previous years can give insights into demand trends. This data analysis enables businesses to prepare for fluctuations by adjusting their inventory levels ahead of time. Collaborating with suppliers can also enhance responsiveness; ensuring that suppliers can accommodate changing demands will aid in maintaining optimal stock levels.
Regulatory Compliance Issues
Regulatory compliance poses yet another significant challenge. The food industry is subject to stringent regulations to ensure safety and quality. Businesses must adhere to guidelines set forth by agencies such as the Food and Drug Administration (FDA). Failing to meet these standards can lead to penalties and reputational damage.
Maintaining accurate records is vital for compliance. A well-implemented inventory management system helps consolidate documentation related to freshness, storage, and handling procedures. This information can be crucial during inspections or audits. Storing records digitally can enhance accessibility and organization, facilitating better management of compliance-related tasks.
In summary, addressing the key challenges in food inventory management involves a multifaceted approach. Solutions must focus on effective tracking of perishables, flexibility to manage seasonal demands, and ensuring compliance with regulations. This strategic focus can enhance overall operational efficiency and contribute positively to a business's bottom line.
"The impact of poor inventory management can cascade through a business, affecting everything from customer satisfaction to regulatory compliance."
Understanding these challenges is the first step toward implementing an effective inventory management system in the food industry.
Components of an Effective Inventory Management System
An effective inventory management system is crucial for the food industry, where factors such as perishability, demand fluctuations, and compliance with regulations play a significant role. Understanding the components of such a system can lead to improved efficiency and better decision-making for businesses. This section focuses on three core elements: inventory tracking features, restocking algorithms, and reporting and analytics tools. Each of these elements contributes to creating a comprehensive inventory management strategy that is adaptable and effective in responding to food industry dynamics.
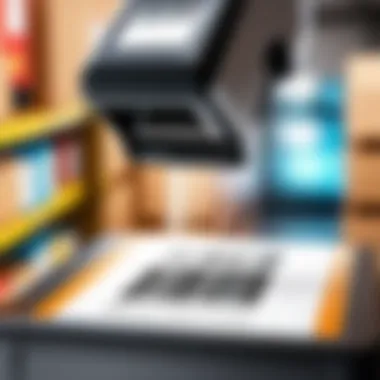
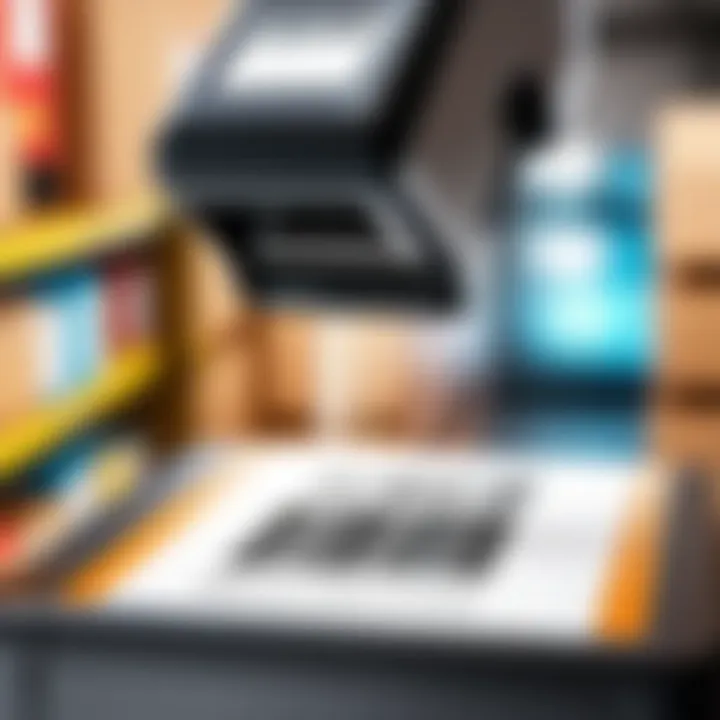
Inventory Tracking Features
Inventory tracking is central to managing stock levels in the food industry. Features that enable precise tracking include barcode scanning, real-time data updates, and automated alerts for low stock levels. By using barcode scanning, employees can quickly and accurately monitor inventory movements, minimizing human error. Real-time data updates ensure that businesses have an accurate view of current stock levels, which is vital for both purchasing and sales decisions.
Moreover, effective inventory tracking allows businesses to monitor product shelf life. Since many food items have a limited lifespan, knowing the expiry dates can reduce waste and optimize usage. This helps maintain freshness and safety standards, which are essential for customer satisfaction and regulatory compliance.
Restocking Algorithms
Restocking algorithms are critical for ensuring that businesses maintain adequate inventory levels without overstocking. These algorithms analyze historical sales data and market trends to predict future demand. By using advanced statistical methods, they can calculate optimal reorder points and quantities, matching supply with actual consumer demand.
Implementing effective restocking algorithms can reduce costs associated with excess inventory. Businesses can benefit from just-in-time inventory practices, which streamline operations and enhance cash flow. Integrating these algorithms with inventory management systems enhances their accuracy and effectiveness, creating a seamless supply chain process.
Reporting and Analytics Tools
Reporting and analytics tools are necessary for making informed decisions in inventory management. Having access to key performance indicators (KPIs) helps identify trends in sales, stock levels, and customer preferences. Tools that provide detailed reports enable businesses to analyze their inventory performance over time. This analysis can help identify slow-moving stock, enabling timely promotions or discounts.
Additionally, advanced reporting features support strategic planning. Businesses can assess the effectiveness of their inventory management practices and make adjustments where necessary. Such analytics foster a proactive rather than reactive business approach, allowing organizations to adapt quickly to market changes.
"A strong inventory management system not only safeguards food quality but also enhances overall operational efficiency."
In summary, an effective inventory management system for the food industry must include reliable inventory tracking features, robust restocking algorithms, and insightful reporting and analytics tools. Together, these components form the foundation that supports efficient operations and informed decision-making.
Types of Inventory Management Systems
Understanding the different types of inventory management systems is crucial for the food industry because each system offers distinct benefits and features. Applying the right system can streamline operations, improve accuracy, and ultimately lead to better financial performance. It's about finding a solution that integrates well with business needs and enhances efficiency.
Traditional Inventory Systems
Traditional inventory systems often rely on manual processes and paper-based records. This method may seem outdated, but it still has its advantages, especially for small businesses. Many operators prefer the simplicity of using spreadsheets or paper logs.
However, the biggest drawback is the potential for human error. Manual entries can lead to inaccuracies. Furthermore, tracking stock levels is time-consuming. As business scales, these methods often prove to be insufficient. Many companies graduate from this approach as they grow.
Benefits of Traditional Inventory Systems:
- Cost-effectiveness: Requires minimal investment initially.
- Familiarity: Staff may find it easier to adapt to familiar methods.
Cloud-Based Solutions
Cloud-based inventory management solutions have been gaining traction in recent years. These systems store data remotely and can be accessed from different locations at any time. For the food industry, this can be particularly useful as it allows businesses to sync inventory data across multiple sites.
In addition, cloud systems can update in real time. This functionality provides an accurate picture of stock levels and helps teams react quickly to changes. The flexibility to scale alongside business needs is another compelling reason to consider this type of system.
Key Features of Cloud-Based Solutions:
- Real-time data access: Keeps everyone informed of current stock.
- Enhanced collaboration: Multiple users can work simultaneously.
- Lower upfront costs: Often offered as a subscription, making it financially feasible.
Mobile Inventory Management Apps
Mobile inventory management apps represent the convergence of technology and convenience. As smartphones become more integrated into daily operations, these apps provide a user-friendly interface for inventory tracking. Staff can conduct stock takes on the go, reducing downtime associated with manual processes.
Mobile applications also come with built-in scanning capabilities. This speeds up logging new stock or adjusting levels, which is especially handy in fast-paced environments like restaurants or warehouses.
Advantages of Mobile Inventory Management Apps:
- Accessibility: Can operate directly from smartphones or tablets.
- Speed: Scanning brings efficiency in updating stock levels.
- User-friendly: Simplifies the training process for staff on inventory protocols.
In summary, understanding the various types of inventory management systems enables food industry professionals to leverage technology effectively. From traditional methods to modern applications, each system has its pros and cons that businesses must weigh carefully.
Implementation Strategies for Success
Implementing an inventory management system in the food industry is not just about selecting software. A well-planned approach is crucial for optimizing efficiency and minimizing disruptions. Successful implementation strategies help ensure that the chosen system aligns with the specific needs of the business. They also address potential roadblocks that could arise during or after the transition.
This section outlines essential strategies for achieving successful implementation of inventory management systems. By understanding business needs, selecting the right technology, and preparing staff for changes, firms can realize the benefits of enhanced inventory management.
Assessing Business Needs
Assessing business needs is the foundation of any successful implementation strategy. This involves a comprehensive evaluation of current processes and the specific demands of the organization. Key elements to consider include:
- Current Inventory Challenges: Identify pain points in the existing system, such as inefficiencies in tracking or challenges in managing perishables.
- Business Goals: Establish clear objectives for what the organization aims to achieve with the new system—whether it's reducing waste, increasing turnover, or adhering to faster delivery times.
- Operational Scope: Analyze the variety of products handled, volume of sales, and frequencies of deliveries. This assessment affects the choice of features required in an inventory management system.
Through this assessment, a business can articulate requirements that inform the selection process. Understanding needs becomes essential to selecting a system that supports growth.
Choosing the Right System
Selecting the right inventory management system is crucial. Businesses encounter various options, including traditional, cloud-based, and mobile solutions. Each type offers unique advantages. When choosing a system, consider the following:
- Scalability: The system should accommodate growth and evolving inventory needs.
- User-Friendliness: A system that is intuitive reduces training time and enhances user adoption.
- Integration Capability: Ensure that the new system can easily integrate with existing tools such as accounting and point-of-sale software.
The key is to analyze features against the assessed business needs. A thorough comparison of different vendors can lead to informed choices that maximize software effectiveness.
Training Staff and Managing Change
Implementing a new inventory management system often involves significant changes in workflows. Therefore, effective training is indispensable. Staff must be equipped not only with the technical know-how but also the confidence to adapt to new procedures. Important strategies include:
- Comprehensive Training Programs: Tailor training to different user groups within the organization. For instance, warehouse staff may need different training compared to management.
- Ongoing Support: Establish a support system for addressing user questions and concerns post-implementation. This helps address any issues that arise swiftly.
- Change Management Strategies: Prepare your team for the transition by communicating benefits, setting clear expectations, and involving them in the implementation process.
"Effective change management can ease the anxiety of new technology and lead to successful adoption across the organization."
These strategies foster an environment that embraces change, leading to better outcomes for the implementation of an inventory management system in the food industry.
Technology’s Role in Inventory Management
In the fast-paced food industry, technology plays a crucial role in ensuring efficient inventory management. With constant fluctuations in supply and demand, managing stock effectively is vital. Implementing advanced technology not only streamlines processes but also reduces waste, enhances freshness, and ultimately leads to cost savings. The integration of technological solutions allows food businesses to maintain optimal stock levels, comply with regulatory standards, and provide better overall service.
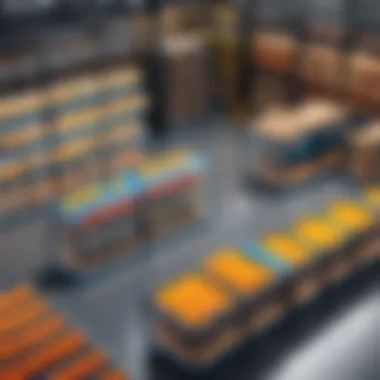
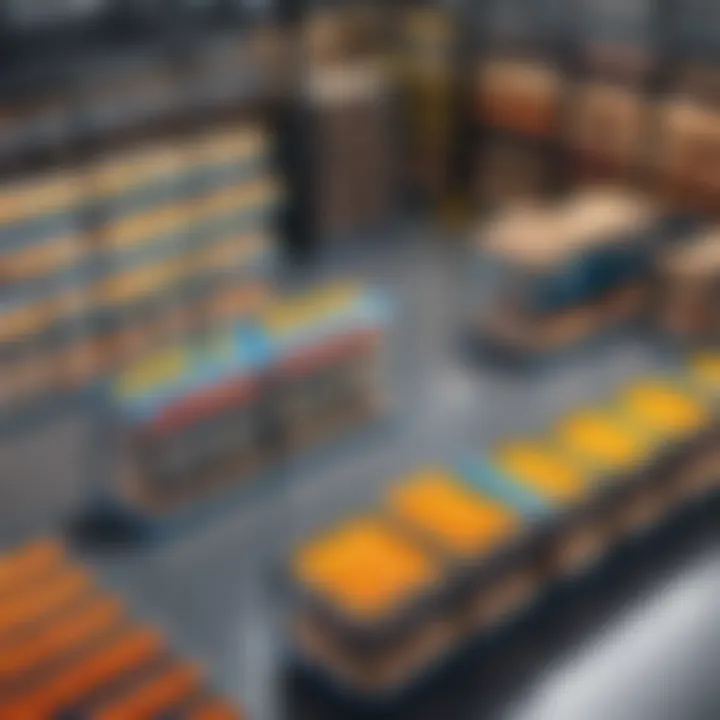
Integration with Other Business Systems
Integrating inventory management systems with other business software is essential for creating a seamless operational flow. Many organizations utilize various platforms for accounting, sales, and supply chain management. When these systems work together, businesses can gain a holistic view of operations. This interconnectedness allows for better data sharing and reduces data duplication.
Benefits of integration include:
- Real-time Visibility: Monitoring inventory levels and sales data in real-time helps businesses make informed decisions quickly.
- Improved Accuracy: Reduces errors in data entry by syncing information across systems.
- Enhanced Reporting: Consolidated data enables detailed reporting and analytics, helping businesses to identify trends and forecast demand accurately.
- Streamlined Processes: Automated workflows between inventory management and sales or accounting speed up operations and improve efficiency.
For example, integrating inventory management with an ERP system, such as SAP or Oracle, facilitates better coordination between departments, ensuring that all units are aligned and correctly informed.
Use of Artificial Intelligence
Artificial Intelligence (AI) is transforming how businesses manage their inventory. The use of AI technologies helps in predicting demand, optimizing stock levels, and enhancing accuracy in inventory records. AI enhances decision-making with analytical insights derived from historical data.
Key applications of AI in inventory management include:
- Demand Forecasting: AI algorithms can analyze historical sales data, seasonal trends, and market conditions to predict future demand more accurately.
- Dynamic Pricing Strategies: Adjusting prices based on real-time demand signals ensures competitiveness and reduces excess inventory.
- Automated Inventory Tracking: AI can automate tasks such as counting stock and monitoring expiry dates, thus minimizing human errors and ensuring compliance with food safety regulations.
Using AI not only enhances efficiency but also allows businesses to focus on strategic planning rather than mundane tasks. Companies leveraging these technologies can respond to market changes swiftly and effectively.
The use of technology in inventory management is not just an option but a necessity for businesses aiming to thrive in the competitive food industry.
The Impact of Regulatory Compliance
Regulatory compliance is a vital aspect of inventory management in the food industry. It encompasses a large set of laws, guidelines, and standards that aim to ensure food safety and quality. Failing to meet these regulations can have serious consequences. These can range from financial penalties to severe damage to a company's reputation. Therefore, understanding and adhering to compliance requirements is paramount for businesses operating in this sector.
One of the most significant benefits of compliance is the assurance it provides to consumers. When customers know a business follows strict regulatory standards, they are more likely to trust its products. This trust can increase customer loyalty and result in repeat purchases. Additionally, companies that adhere to regulations tend to have better operational efficiencies. They may avoid costly recalls and wastage, benefiting their bottom line.
Incorporating compliance into inventory management processes also helps streamline operations. Businesses must regularly review and update their practices to align with the latest regulations. This can lead to a more organized and systematic approach to handling inventory. By embedding compliance within their systems, organizations can improve traceability and accountability throughout the supply chain.
"Compliance is not just about avoiding penalties. It is an essential part of trustworthy business practices that fosters consumer confidence."
Understanding Food Safety Regulations
Food safety regulations serve as the foundation for ensuring that food products are safe for consumption. Different countries have established various regulatory bodies to enforce these laws. For example, in the United States, the Food and Drug Administration (FDA) oversees food safety standards. These regulations cover everything from sourcing ingredients to the handling, processing, and distribution of food products.
Relevant regulations typically include guidelines on hazardous materials, allergens, and proper labeling. Businesses must ensure that their inventory management systems can track necessary information about each product. This includes expiration dates, lot numbers, and storage conditions. Failure to monitor these elements can result in severe consequences, including health risks for consumers.
Furthermore, regular training for staff on food safety regulations is essential. Employees need to be aware of the procedures and practices that maintain compliance. This training reduces the chance of human error, which can lead to non-compliance.
Documentation and Reporting Requirements
Accurate documentation and reporting are crucial in maintaining regulatory compliance. Companies in the food industry are required to keep detailed records that demonstrate compliance with safety regulations. These documents may include purchase orders, shipping manifests, and quality control reports.
An effective inventory management system can automate the documentation process. Doing so reduces human error, saves time, and ensures accuracy. Companies must be able to generate reports quickly in case of an audit or inspection. Responsive systems are key here, as they provide real-time data for regulators to review.
Moreover, documentation is not just for regulatory bodies. It also serves internal purposes. An organization can evaluate inventory turnover rates and identify areas for improvement. Regularly reviewing documents can help streamline operations and enhance overall efficiency.
Ultimately, while compliance may seem burdensome, it is an indispensable part of the food industry. Its implications reach far beyond regulatory authorities, significantly impacting customer trust, branding, and overall business success.
Evaluation of Top Inventory Management Solutions
In any food-related business, the selection of an appropriate inventory management solution can determine operational efficiency and customer satisfaction levels. The food industry is plagued with unique challenges such as perishability, regulatory compliance, and varying demand. Hence, evaluating software options meticulously is crucial. This section aims to provide insights into effective evaluation strategies, focusing on identifying the most suitable systems that may enhance productivity and ensure compliance with industry regulations.
Overview of Leading Software Options
When contemplating the adoption of an inventory management system, it is imperative to consider several guiding factors. Not all software packages are designed with the nuances of the food industry in mind. Leading options like Fishbowl, and Inventory Planner, and other established software solutions offer tailored features that cater to food management.
A few features to look out for include:
- Inventory Tracking: The capability to monitor stock levels in real-time.
- Supplier Management: Assistance in organizing supplier contracts and communication.
- Order Management: Streamlined processes for product orders and sales.
Additionally, several cloud-based solutions ensure instant access to necessary information, allowing operators to check stock levels from any location.
Comparison of Features and Pricing
Comparing features across different inventory management platforms can clarify which software best aligns with business demands. Not only is it important to scrutinize functionality, but pricing also plays a decisive role. Here are some aspects to consider while comparing:
- Usability: Look for an intuitive user interface that enhances staff productivity rather than hinder it.
- Scalability: Determine if the software can expand with the business growth.
- Integration: Verify how well the software communicates with existing systems, such as accounting or customer relationship management.
Pricing Overview
The pricing model may vary significantly. Some systems operate on a subscription basis, while others require a lump sum payment. Consider also maintenance costs and update fees. Inquiries into the trial period can provide essential insights into software performance before a commitment is made.
It is essential to take a holistic view when evaluating your options. This will aid in making an informed decision that could directly impact operational success in the food industry.
Best Practices in Food Inventory Management
Efficient inventory management is critical in the food industry due to the unique challenges it faces. Best practices enhance operational efficiency, ensure compliance, and improve overall profitability. Adopting these practices not only reduces waste but also improves customer satisfaction through better product availability.
Regular Audits and Assessments
Regular audits and assessments of inventory help maintain accuracy and minimize discrepancies. These evaluations serve as a proactive measure to identify potential issues before they escalate. Maintaining an accurate account of inventory levels is essential, particularly for perishable goods. With frequent assessments, businesses can ensure that stock levels align with demand.
Capturing data during these audits involves examining expiration dates, checking stock rotation, and identifying slow-moving items. This information is valuable for making informed decisions about the stock. Implementing a robust schedule for audits helps maintain traceability, which is crucial for compliance with food safety regulations. A structured approach to inventory audits enables businesses to refine their inventory strategies regularly.
Data-Driven Decision Making
Data-driven decision making is essential in optimizing inventory management. Businesses can analyze historical sales data to predict future demand more accurately. This approach allows for more informed purchasing decisions and manages stock levels effectively. Through data, companies can also identify trends, such as seasonal fluctuations in demand for specific food items, helping them adjust inventory accordingly.
Furthermore, adopting analytics tools can help track product performance over time. Integrating data from different departments, such as sales and marketing, fosters a holistic view of inventory needs. This interconnectedness allows businesses to deploy resources strategically and minimize waste. It enhances the capacity of management to respond effectively to changing market conditions.
Sustainability Considerations
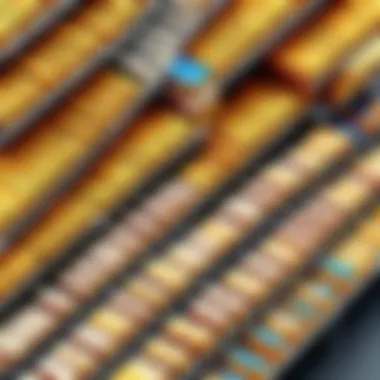
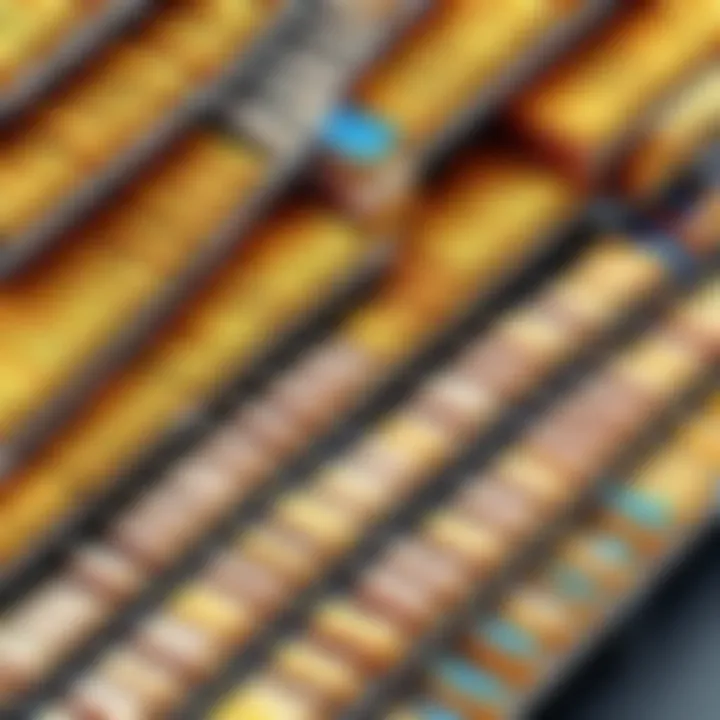
Sustainability is becoming increasingly important in the food industry. Adopting sustainable inventory practices not only meets consumer demands but also reduces environmental impact. This involves practices such as minimizing food waste, sourcing from sustainable suppliers, and implementing efficient supply chain practices.
Businesses can implement systems that track the lifecycle of inventory, facilitating better decision-making for waste reduction. For example, restaurants can analyze waste patterns to adjust purchasing habits. This reflects a commitment to sustainability while also enhancing profitability. Overall, creating a sustainable inventory management system aligns with broader environmental goals and enhances brand reputation.
"Sustainable practices in inventory management not only help the environment but can also improve a company's bottom line."
Emerging Trends in Inventory Management
Emerging trends in inventory management are crucial for businesses, particularly in the food industry. These trends influence how companies operate, adapt, and remain competitive. It is essential to understand these trends to leverage their benefits effectively. They not only shape internal processes but also enhance the supply chain’s efficiency. Focusing on the right trends can lead to improved accuracy, reduced waste, and greater compliance with regulations.
Blockchain Technology
Blockchain technology is increasingly relevant in inventory management. This technology offers enhanced tracking and transparency of products throughout the supply chain. Each transaction is recorded on a decentralized ledger, allowing all parties to verify the history of a product. This can be especially beneficial for the food industry, where safety and traceability are paramount.
Advantages of Using Blockchain:
- Increased Transparency: Every change in inventory status is logged, which can help validate freshness and authenticity.
- Improved Traceability: In case of a food safety issue, blockchain enables quick identification of the source, aiding in rapid response actions.
- Reduced Fraud: By securing information on blockchain, the risk of fraud is minimized. This solidifies supplier relationships and consumer trust.
Despite its potential, there are considerations like the initial implementation cost and the need for training staff to navigate the new system. However, the long-term advantages can offset these initial challenges.
Automation and Robotics
Another significant trend shaping inventory management is automation and robotics. Automation streamlines operations, reducing human error and increasing efficiency by minimizing time spent on manual tasks. Robotics can assist in various functions, including sorting, storing, and transporting goods.
Benefits of Automation and Robotics:
- Enhanced Efficiency: Automated systems can process inventory faster than manual methods; this efficiency can lead to significant time savings.
- Better Accuracy: Automated systems reduce chances of errors in inventory counts and ordering.
- Cost-Effectiveness: Although initial investments for robotics may be high, the ongoing operational savings can be substantial.
Adopting robots and automated solutions might require a change in workforce skills. Staff may need training to work alongside these technologies. Nonetheless, the ultimate goal of improved operational efficiency is well worth the effort.
"Emerging trends such as blockchain and automation address some of the most pressing challenges in inventory management, positioning firms for future success."
Case Studies and Success Stories
Case studies provide tangible evidence of successful inventory management system implementations within the food industry. They illustrate real-world applications of theory, showcasing how companies navigated unique challenges using specific systems. Success stories not only validate the effectiveness of particular inventory strategies but also serve as learning tools for others in the industry. They can highlight aspects like efficiency gains, cost reductions, and improved compliance with food safety regulations. By analyzing these case studies, businesses can draw insights into the practicalities of implementation.
Benefits of Case Studies
- Show Real Results: They present measurable outcomes that can guide other businesses.
- Highlight Best Practices: Successful examples outline methods and approaches that are effective in similar scenarios.
- Illustrate Technology Integration: They reveal how different technologies have been leveraged for success in inventory management.
In summary, the case studies and success stories of the food industry offer a wealth of knowledge that can assist businesses in selecting the right inventory management solutions and frameworks. They provide a platform for learning about best practices while simultaneously helping in understanding sector-specific challenges.
Examples from Major Food Producers
Major food producers often set benchmarks through their innovative inventory management approaches. For instance, Nestlé has successfully integrated cloud-based inventory systems that provide real-time data analytics. This allows them to manage their vast inventory efficiently, decreasing waste due to perishability.
Another notable example is Walmart, which employs sophisticated inventory management techniques that allow them to maintain optimal stock levels across their stores. Their use of predictive analytics helps anticipate seasonal demand, ensuring popular food items are always available.
These examples illustrate that large-scale operations benefit from leveraging technology to improve inventory accuracy and response times. By adopting proven inventory processes, these producers achieve substantial improvements in operational efficiency.
Lessons Learned from Implementation
The implementation phase of inventory management systems is a critical juncture. One major insight is that comprehensive training and change management are essential. Food industry players like Coca-Cola have emphasized the importance of equipping employees with the necessary skills to utilize new systems effectively. Their experience shows that when staff understand the technology better, they are more likely to use it to its full potential.
Additionally, accurate data entry proved significant in several case studies. For instance, incorrect inventory tracking can lead to overstocking or stockouts, impacting revenue and customer satisfaction. Companies learned to prioritize rigorous data verification processes before and after implementation.
Here are some key lessons businesses have drawn from various implementations:
- Input Accuracy: Establish processes for double-checking and verifying data inputs.
- Employee Training: Invest in ongoing training programs to keep staff updated on best practices.
- Continuous Review: Regular audits of inventory practices inform necessary adjustments to systems.
The Future of Inventory Management in the Food Industry
The management of inventory in the food industry is evolving rapidly. As we look to the future, several key factors emerge that will significantly shape how businesses approach their inventory systems. The advancements in technology, changing consumer preferences, and an emphasis on sustainability will drive innovations in inventory management. These developments offer important benefits but also come with considerations that must be addressed.
Potential Innovations
Several potential innovations can redefine inventory management in this sector.
- Artificial Intelligence and Machine Learning
AI can enhance forecasting accuracy by analyzing historical data to predict demand patterns. It can also streamline restocking processes, optimizing inventory levels to reduce waste. - Internet of Things (IoT)
Devices connected through IoT can track inventory in real time, providing insights into stock levels and enabling better decision-making. For example, temperature sensors can monitor perishables, ensuring they are stored correctly. - Blockchain Technology
Blockchain can improve traceability and transparency in the supply chain. It allows stakeholders to verify the details of each transaction, fostering trust and compliance with food safety regulations. - Mobile Applications
With the prevalence of smartphones, mobile apps can provide a way for companies to manage inventory on-the-go. This flexibility enhances efficiency and responsiveness. - Robotics and Automation
Automated systems for inventory picking, packing, and management can reduce labor costs and increase accuracy in handling goods. Robotics technology is becoming more accessible and affordable for food businesses.
The incorporation of these innovations can lead to better efficiency, lower costs, and more agile inventory management.
Long-Term Predictions
Looking ahead, several long-term predictions can be made regarding inventory management in the food industry.
- Increased Use of Data Analytics
Businesses will rely more on data analytics to make informed decisions. This trend will enable better understanding of consumer behavior and market trends. - Adoption of Sustainability Practices
The emphasis on sustainability will grow. Companies may prioritize methods that reduce food waste and enhance eco-friendliness in their inventory practices. - Enhanced Regulatory Compliance
As regulations continue to evolve, companies will need to integrate compliance features into their inventory systems. This integration will help avoid costly penalties and ensure adherence to safety standards. - Global Supply Chain Management
As markets become more interconnected, companies will need to develop strategies for managing global supply chains. This complexity will necessitate sophisticated inventory management systems capable of handling varied challenges across different regions. - Collaboration and Partnerships
Food companies may increasingly seek partnerships with technology providers and logistics firms to leverage expertise and improve inventory accuracy and efficiencies.
The trajectory of inventory management in the food industry is directed towards a more technologically integrated, efficient, and sustainable future. As various elements come together, the choices made today will dictate the success of businesses in navigating these changes.
Ending
The conclusion of this article holds significant importance as it encapsulates the entire discussion around inventory management systems tailored for the food industry. This section serves as a synthesis of the key points presented throughout the article, highlighting essential elements that decision-makers must consider in their approach to inventory management.
Summary of Key Insights
In reviewing the various sections, it is clear that effective inventory management is critical for maintaining product quality and compliance with safety regulations. Key insights include:
- Perishability Challenges: Food products have a limited shelf life. Understanding perishability is crucial in minimizing waste and ensuring freshness.
- Seasonal Demand Fluctuations: The food industry experiences varying demands based on seasons. Monitoring inventory must align with these changes.
- Regulatory Compliance: Keeping up with food safety regulations is not only a legal requirement but also essential for building consumer trust.
- Technological Adaptation: Embracing technology, such as artificial intelligence and cloud-based solutions, enhances inventory tracking and decision-making processes.
- Best Practices Implementation: Regular audits, data-driven decisions, and sustainability efforts can lead to improved efficiency and cost savings.
"An organization with a solid inventory management strategy is more likely to respond effectively to both market changes and unexpected challenges."
Final Recommendations
In concluding, the following recommendations can guide food industry stakeholders:
- Assess Specific Needs: Each business has unique requirements. Conduct a thorough assessment before choosing an inventory management system.
- Invest in User-Friendly Technology: Select software that is both efficient and easy for staff to adopt. The learning curve should be manageable.
- Prioritize Compliance Training: Ensure employees are well-trained on compliance requirements to avoid costly penalties.
- Utilize Real-Time Data: Make use of systems that offer real-time tracking and reporting functionalities to make informed decisions.
- Stay Informed on Trends: Keep abreast of emerging technologies such as blockchain and automation that could impact inventory management strategies.
In summary, understanding and implementing effective inventory management systems can significantly enhance operational efficiency, reduce waste, and ensure regulatory compliance in the food industry. Collectively, these insights and recommendations equip organizations to make informed and strategic decisions.