Comprehensive Guide to Diesel Mechanic Shop Software

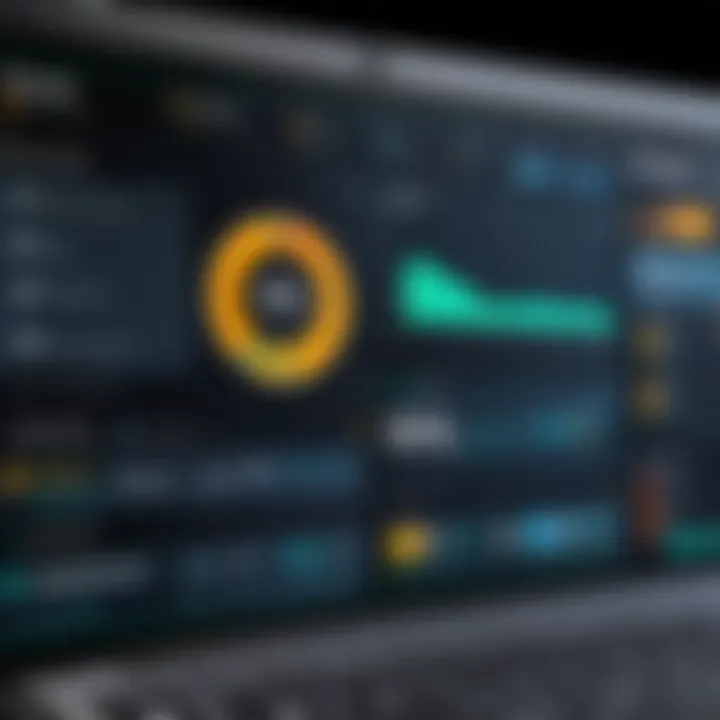
Intro
The landscape of diesel mechanic shops is rapidly evolving in the face of technological advancements. Diesel mechanic shop software is no longer just a luxury but a necessity for enhancing operational efficiency and profitability. Understanding how to assess software needs is the first step for mechanics and business owners navigating this landscape. Identifying user requirements and evaluating existing software solutions will reveal the strengths and gaps in current offerings, setting the stage for informed decision-making.
Software Needs Assessment
Identifying User Requirements
A crucial starting point for any business considering diesel mechanic shop software is identifying user requirements. This involves understanding both the workflow of the shop and the specific needs of the users. Interviews and surveys with mechanics, office staff, and management can yield valuable insights.
In addition, it is essential to consider the following factors:
- Type of Services Offered: Different shops may have unique requirements based on the service types they provide.
- Number of Users: The software should comfortably accommodate all users, from mechanics to administrative personnel.
- Desired Features: These may include job scheduling, invoicing, inventory management, and customer relationship management tools.
Evaluating Current Software Solutions
Once requirements are identified, evaluating current software solutions is paramount. An exhaustive analysis of available software can highlight which options are best aligned with the shop's needs. Pay close attention to:
- User Interface: A user-friendly interface increases efficiency and reduces the learning curve.
- Integration Capabilities: Ensure the software can integrate with other tools used by the shop, such as accounting or inventory management systems.
- Customer Support: Reliable customer support is critical, especially during the implementation phase.
> "The most successful shops assess their unique needs before seeking software solutions."
Data-Driven Insights
Market Trends Overview
Staying abreast of market trends is vital for making informed choices about software. Currently, trends indicate a growing inclination towards cloud-based solutions. These systems offer flexibility, allowing users to access data from various locations. Additionally, there is an increase in the use of mobile applications that enable on-the-go management of shop operations.
Performance Metrics
Having performance metrics is beneficial to gauge how well the software meets user needs. Key metrics might include:
- Efficiency Improvements: Measure the time taken for specific tasks before and after software adoption.
- Customer Satisfaction: Regularly assess customer feedback and satisfaction rates.
- Cost Savings: Analyze how software impacts overhead costs and labor efficiency.
In summary, fueling decision-making with data-driven insights empowers diesel mechanic shops to select software that not only meets their current needs but also supports future growth and innovation.
Prelims to Diesel Mechanic Shop Software
The role of diesel mechanic shop software is increasingly significant in todayโs automotive landscape. As the diesel repair industry evolves, shop owners and mechanics find themselves challenged by rising operational demands and customer expectations. In this context, understanding the functionalities and benefits of specialized software solutions becomes essential.
Diesel mechanic shop software serves as a comprehensive tool designed to streamline operations, from managing work orders to tracking inventory. This type of software offers critical features such as billing, invoicing, and customer relationship management (CRM), which are vital for enhancing shop efficiency.
Some key factors contribute to the importance of diesel mechanic shop software:
- Operational Efficiency: By automating routine tasks, the software reduces the time mechanics spend on administrative work. This enhances productivity and allows for focusing more on repairs and maintenance tasks.
- Accuracy in Record Keeping: Maintaining accurate records is crucial in the diesel mechanic field. The software enables precise documentation of services rendered, parts used, and customer communications, mitigating errors prevalent in manual processes.
- Customer Satisfaction: As customers demand faster service and updates, having the right tools can positively influence their experience. Software can provide timely information regarding service status, thus improving customer relations.
Additionally, the integration of emerging technologies, such as mobile solutions and cloud computing, is reshaping the traditional practices within diesel shops. The flexibility that comes with these technological advancements allows for better scalability and adaptability to various business models.
A software solution tailored for diesel mechanics does not just simplify existing processes. It actively transforms how shops operate, enabling them to respond more swiftly to changing market demands. In essence, the introduction of diesel mechanic shop software marks a significant step towards modernizing repair operations and enhancing overall efficiency.
"Investing in specialized software is not just about keeping up; itโs about staying ahead in an evolving industry."
This article will delve deeper into understanding the specific needs of diesel mechanic shops, the software features that can meet these needs, and the broader implications for the industry. By examining these elements, readers will gain insights necessary to make informed decisions regarding software that aligns with their operational goals.
Understanding Software Needs in Diesel Mechanics
The selection of appropriate software is paramount for any diesel mechanic shop aiming to optimize its operations. Understanding the unique software needs within the diesel mechanics industry allows shop owners to tailor their choice of tools effectively. This section delves into the fundamental elements that underscore the necessity of aligning software capabilities with operational requirements.
Identifying Core Operational Processes
In any diesel mechanic shop, core operational processes are the lifeblood of effective mechanics. These include work order management, inventory control, scheduling, and customer interactions. Each process interacts and relies on software tools for tracking and execution. A clear understanding allows business owners to select software that efficiently supports these integral operations.
For instance, an effective work order management system streamlines the assignment of jobs to technicians, tracks progress, and facilitates communication with customers. A strong inventory management feature prevents stock shortages, ensuring parts are always available when needed. Therefore, identifying these core processes is crucial in establishing the foundation for selecting software that enhances overall productivity and customer satisfaction.
Assessing Customer Service Requirements
Customer service plays a vital role in the success of diesel mechanic shops. Aspects of customer interaction can greatly affect repeat business and overall reputation. Assessing what is needed in terms of customer service requires an understanding of client expectations and preferred communication patterns.
The software should support efficient customer relationship management (CRM) features. This includes the ability to track interactions, follow up on service history, and manage appointments. Providing timely updates about repairs and service offers enhances customer experiences significantly.
Moreover, excellent software can enable meaningful data analytics. Being able to analyze past customer trends provides insights into preferences and allows for tailored marketing. In essence, assessing customer service requirements prepares shop owners to choose software that fosters loyalty and strengthens client relationships while improving operational efficiency.
Key Features of Diesel Mechanic Shop Software
The significance of key features in diesel mechanic shop software cannot be understated. These functionalities streamline operations, enhance communication, and improve overall efficiency in managing daily tasks. Each feature represents a building block in the software, contributing to a successful integration that meets the unique demands of diesel repair shops.
Inventory Management
A robust inventory management system is crucial for any diesel mechanic shop software. It allows mechanics and shop owners to keep track of parts, tools, and equipment. The visibility into inventory levels can prevent over-ordering and stockouts, ultimately saving money.
Benefits of effective inventory management include:
- Real-time tracking of parts availability.
- Automated reorder notifications to ensure necessary items are always in stock.
- Insights into usage patterns, which aid in effective budgeting.
As diesel mechanics often need specific parts for repairs, this feature supports operational continuity and enhances service delivery.
Work Order Management
Work order management is another vital feature that allows for the efficient tracking of jobs from start to finish. This component helps in organizing tasks by assigning them to specific employees and tracking progress.
Considerations when evaluating work order management include:
- The ability to customize work orders based on specific customer needs.
- Ease of tracking time spent on jobs, enabling accurate billing.
- Integration with other software components for seamless workflow.
A good work order management system enhances overall productivity by ensuring that jobs are completed on time and in accordance with customer expectations.
Billing and Invoicing
Billing and invoicing is a critical aspect of any business operation. In diesel mechanic shop software, this feature automates the financial transactions involved in service delivery.
Benefits include:
- Simplified billing process that reduces errors.
- Generation of detailed invoices that clearly itemize services and parts.
- Easy management of payments and account history for customers.
Automation of these tasks minimizes the administrative burden on staff, allowing them to focus more on servicing vehicles rather than dealing with paperwork.
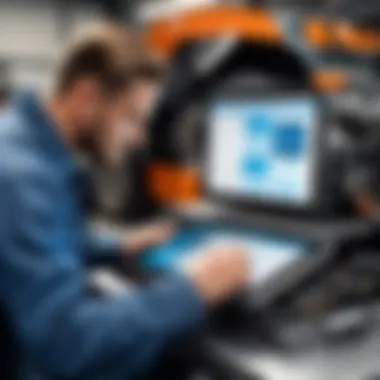
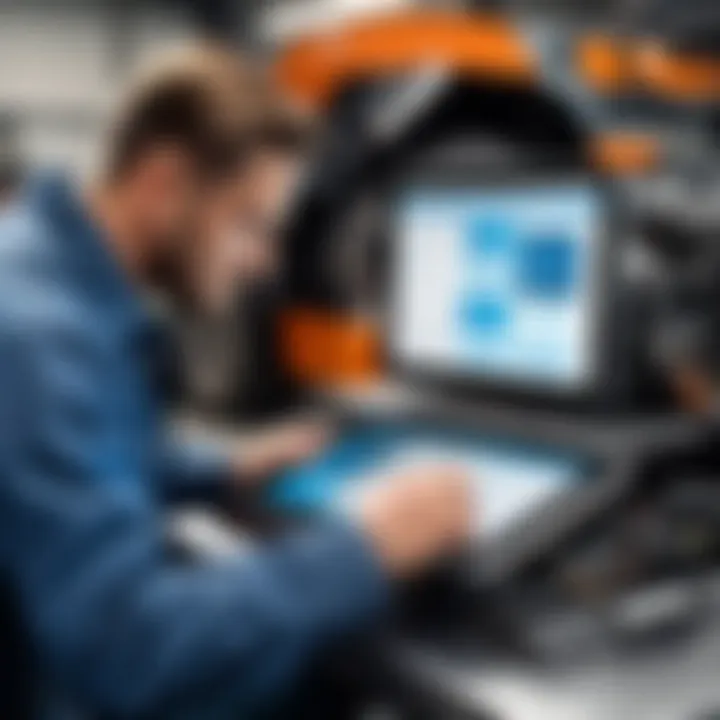
Customer Relationship Management (CRM)
Customer Relationship Management (CRM) is an essential feature that facilitates the management of customer information and interactions. This feature enables diesel shops to maintain strong relationships with clients.
Key aspects of CRM features are:
- Centralized customer database that holds contact details, service history, and preferences.
- Automated follow-ups and reminders for servicing schedules or after-service feedback requests.
- Tools for analyzing customer data to improve services and marketing efforts.
Having a CRM integrated within diesel mechanic shop software can significantly enhance customer satisfaction and loyalty while fostering a more personalized service approach.
"Effective shop management involves more than just fixing trucks; it requires understanding inventory, scheduling, billing, and customer relations together in one cohesive system."
Benefits of Implementing Diesel Mechanic Shop Software
In the context of diesel mechanic shops, software implementation brings numerous advantages. As the industry evolves, reliance on technology becomes essential for competitive survival. Having the right software can greatly impact operational performance. Understanding the specific benefits can help shop owners decide on the appropriate tools for their business.
Increasing Efficiency
Efficiency drives profitability in a diesel mechanic shop. Software solutions streamline various processes. For instance, work order management systems can automate task assignments, ensuring that mechanics focus on their jobs instead of administrative duties. This reduces wait times and improves workflow. When tasks are organized electronically, the time spent searching for information decreases significantly.
Moreover, features like automated parts ordering can help shops maintain optimal inventory levels. Tools that analyze usage data allow for precise stock control. Thus, mechanics are less likely to experience delays due to unavailable parts.
Enhancing Accuracy in Record Keeping
Accurate record-keeping is vital. Diesel mechanic shop software reduces human error that often occurs with manual data entry. By utilizing digital records, shops ensure that customer histories, service details, and parts inventory are always up-to-date. This can facilitate compliance with industry regulations and standards.
In addition, these software solutions often include reporting features. Detailed analytics can provide insights into shop operations. For instance, performance metrics help identify areas for improvement. Accurate records can also simplify financial audits, as all transactions and activities are documented systematically.
Improving Customer Satisfaction
Customer satisfaction is the bedrock of any successful business. Diesel mechanic shop software enhances this aspect by facilitating better communication. Automated appointment reminders and follow-up messages can keep customers informed, ultimately improving their experience. When customers feel valued and informed, likelihood of repeat business increases.
Furthermore, efficient service delivery translates to quicker turnaround times for repairs. When shops operate at their peak efficiency due to software support, customers receive their vehicles back faster. Satisfied customers are likely to leave positive reviews, which are critical for reputation in the competitive market.
The Role of Automation in Diesel Mechanic Shops
Automation plays a significant role in enhancing the operational efficiency of diesel mechanic shops. It streamlines various processes, leading to time and cost savings. As the industry advances, integrating automated systems becomes increasingly essential. These systems aid in minimizing human error, improving accuracy, and optimizing overall workflow. Automation allows staff to focus on high-priority tasks while routine jobs are handled by software solutions.
Automating Routine Tasks
Routine tasks in a diesel mechanic shop, like invoicing and scheduling, often consume valuable time. Automating these tasks reduces the burden on mechanics and administrative staff. For instance, invoicing software can expedite billing procedures, making the process quicker and more efficient. Automation software can also manage appointments and remind both customers and staff about scheduled services. This minimizes miscommunications and helps maintain a smooth workflow.
Benefits of automating routine tasks include:
- Increased efficiency in day-to-day operations
- Reduction in human error, enhancing accuracy
- Allowing mechanics to dedicate their skills to more complex tasks
By freeing up resources, shops can improve service quality and overall customer satisfaction.
Streamlining Communication
Effective communication is vital in managing a diesel mechanic shop. Automation tools enhance communication both internally among staff and externally toward customers. For example, software solutions can streamline communication by enabling real-time updates on job statuses. Technicians can notify service advisors of delays or progress without needing to verbally relay the information, which can often be misinterpreted.
Additionally, automated communication can engage customers through alerts and confirmation messages. This ensures that customers are informed about their vehicle's repair status, leading to higher levels of trust and satisfaction.
Key points on how automation streamlines communication:
- Facilitates quick information sharing among team members
- Provides timely updates to customers, enhancing transparency
- Allows for better workflow management by tracking tasks and deadlines
Integrating these systems can help shops operate more smoothly, ultimately benefiting the bottom line and enhancing customer experiences.
Market Trends Influencing Diesel Mechanic Software
In the rapidly evolving landscape of diesel mechanic shop software, understanding market trends is critical for shop owners and managers. These trends not only shape the functionality and development of the software, but also influence the way diesel repair shops operate and interact with their customers. Staying attuned to these trends enables stakeholders to make informed decisions that align with current and future demands in the industry.
Integration of Mobile Technology
Today, mobile technology has become an integral part of the automotive repair industry, including diesel mechanic shops. The availability of mobile applications allows mechanics to access information while on the move. This capability provides greater flexibility and enhances productivity. For example, mechanics can update work orders, check inventory, or even communicate with customers directly via mobile apps. By integrating mobile technology, shops can manage their operations more effectively and ensure that mechanics have the necessary tools at their fingertips.
Key benefits of mobile technology integration include:
- Real-time access to information
- Improved communication between shop staff and customers
- Enhanced visibility into daily operations
- Streamlined processes through mobile invoicing and payments
"Mobile technology is not just a convenience; it enhances the overall workflow and operations of diesel mechanic shops."
Cloud Computing Solutions
Cloud computing solutions are gradually transforming how diesel mechanics manage their shop's data and processes. Storing information in the cloud means that shops can access vital data from anywhere, reducing the reliance on physical servers. This shift offers numerous advantages, including better data security, increased storage capabilities, and enhanced collaborative features.
By implementing cloud-based software solutions, shops can experience:
- Scalability, allowing them to grow without significant infrastructure investments
- Cost-effectiveness, as operations can shift from a capital expense model to a more manageable subscription model
- Improved backup and recovery, ensuring that critical data remains safe and accessible at all times
As these technologies advance, diesel mechanic shops must evaluate how cloud solutions can fit into their operational strategy.
In summary, the integration of mobile technology and cloud computing solutions marks a significant trend in diesel mechanic shop software. Both technologies offer unique advantages that can lead to greater efficiency, enhanced customer satisfaction, and overall operational improvement.
Factors to Consider When Choosing Software
Selecting the right diesel mechanic shop software is a critical decision. The software that you choose directly impacts your operational efficiency, customer satisfaction, and ultimately, your bottom line. Understanding the factors that influence this choice is essential for maximizing these benefits and ensuring the right fit for your shop's specific needs.
Scalability and Flexibility
Scalability refers to the software's ability to grow with your business. As your shop expands, you may need to handle more customers, more complex transactions, or additional locations. A scalable software solution can adapt without the need for a complete overhaul. Flexibility complements scalability by allowing customization. Some shops might require specialized features that align with their unique processes. This adaptability can include interface customization and feature add-ons, ensuring that the software evolves alongside the business.
Key points regarding scalability and flexibility include:
- Future Growth: Choose software that can manage increased inventory and employee workloads.
- Customization Options: Examine if the software can be tailored to meet specific operational requirements.
- User Capacity: Ensure the software can support an increasing number of users and devices.
Cost of Implementation
Cost is a significant consideration when selecting software. The initial investment is often a straightforward part of this decision, involving license fees, installation charges, and possible hardware upgrades. However, it's crucial to look beyond upfront costs. Consider ongoing expenses such as subscription fees, potential maintenance costs, and training expenses.
Long-term financial implications can affect your shopโs profitability. An expensive software package might seem appealing due to advanced features, but it may not be practical. Assess how the cost structure aligns with your budget and the expected return on investment.
When analyzing cost, consider:
- Initial Costs: What is the initial price and what does it include?
- Recurring Costs: Are there ongoing fees or potential costs for updates and maintenance?
- ROI: Can the software save money or enhance revenue in a way that justifies its costs?

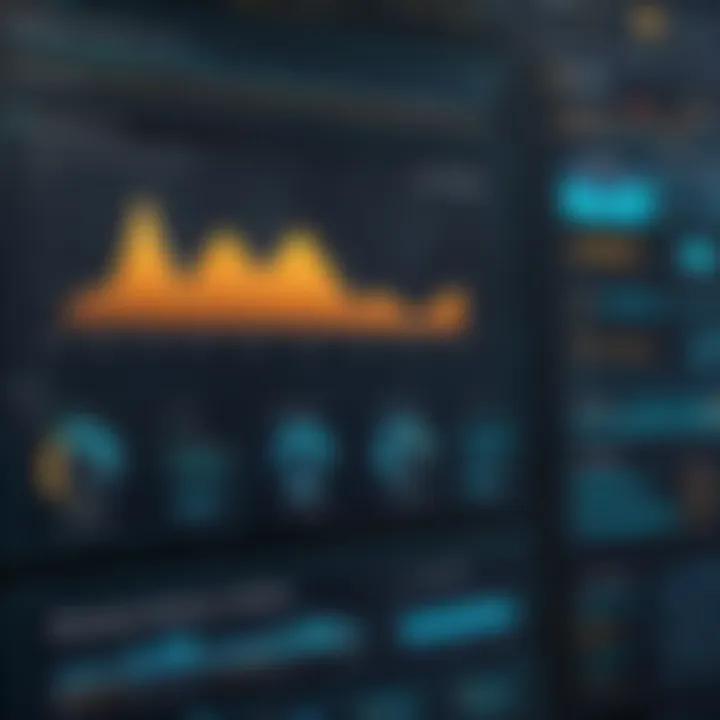
User Support and Training
No matter how advanced a software system may be, without adequate user support and training, it can quickly become a burden. Look for software that offers comprehensive support options โ such as 24/7 helpdesks, extensive user guides, and tutorial videos. Complicated software can lead to frustration among users, which can reduce productivity.
Training is equally vital. Many software vendors provide initial training, but it's essential to investigate how ongoing training is managed, especially as updates are released. Regular training keeps staff proficient, ensuring that your shop reaps maximum benefits from the software.
Consider the following when evaluating support and training:
- Availability of Support: What are the hours of customer support and how can you contact them?
- Training Resources: What training programs are available for new users and ongoing learning?
- Community Support: Is there an online community or forum for additional user support?
"Investing in good software without the corresponding user support is like buying an advanced piece of machinery lacking the necessary operators."
Understanding these factors will greatly enhance the decision-making process in your quest for the most suitable diesel mechanic shop software.
User Experiences and Testimonials
In the realm of diesel mechanic shop software, user experiences and testimonials offer crucial perspectives. They provide real-life insights into how software impacts daily operations. Understanding these experiences can serve as a vital component of the decision-making process for potential users. By examining how existing users interact with the software, one can identify its strengths and weaknesses, which influences choices significantly.
Testimonials reveal how effectively the software meets the specific needs of diesel mechanics. These accounts often highlight practical applications, usability, and overall satisfaction with the features offered. Moreover, they give a glimpse into the actual return on investment, which is important for any business owner. An understanding of user experiences can guide new users to avoid common pitfalls and ensure optimal utilization of the software.
Case Studies from Successful Shops
Examining case studies from successful diesel mechanic shops provides a more in-depth understanding of the practical use of software solutions. These case studies often highlight the journey of shops before and after software implementation. For instance, a shop that adopted Mitchell 1 ProDemand saw significant enhancements in operational efficiency. Employees reported a 30% decrease in time required for parts ordering and customer follow-ups.
Another case study worth noting is a multi-location repair shop that integrated Shop-Ware. This led to streamlined communication processes, which in turn boosted team collaboration. The shop recorded a 25% increase in productivity within months, directly linked to effective software use. Such examples empower new users to visualize potential benefits and inform their software selection decisions.
Common Success Metrics
When evaluating the effectiveness of diesel mechanic shop software, businesses often consider specific success metrics. These metrics provide an objective basis for measuring improvements. Here are some common metrics to consider:
- Efficiency Gains: Tracking the time taken for various processes pre- and post-software implementation.
- Revenue Growth: Monitoring sales figures over time to determine the financial impact.
- Customer Satisfaction: Utilizing surveys and feedback mechanisms to capture client experiences and satisfaction levels.
- Work Order Completion Rates: Assessing the volume of completed jobs against the expected rates to gauge productivity.
- Employee Performance: Evaluating how the software impacts staff performance and task management efficiency.
Ultimately, understanding these metrics allows shops to measure success effectively. They create a benchmark for continuous improvement and help identify areas needing attention. As shops consider new software, incorporating real user experiences enriched by these metrics can guide them towards a more informed decision.
Comparative Analysis of Available Software Solutions
Understanding the various software solutions for diesel mechanic shops is critical for making informed decisions. With numerous options available on the market, a comparative analysis provides the framework to assess their capabilities, pricing, and overall value. This section will explore popular software options, examining their features as well as their strengths and weaknesses. Such an analysis aids shop owners in identifying the software that aligns with their specific operational needs.
Overview of Popular Software Options
Many software options cater to the unique demands of diesel mechanic shops. Some notable examples include:
- Shop-Ware: Known for its user-friendly interface and strong customer support, it provides robust work order management and point-of-sale features.
- Mitchell 1: This option offers integrated repair information, alongside service management tools, making it ideal for mechanics looking for detailed insights.
- RepairShopr: A complete business management tool, it integrates parts ordering, customer management, and invoicing, among other features.
- ProDemand: A software focused on providing vehicle repair information, diagnostics, and labor guides, it is useful for enhancing repair efficiencies.
Each of these software solutions delivers distinct functionalities that can greatly benefit diesel mechanic operations. The choice ultimately depends on the specific requirements of a shop and its operational goals.
Strengths and Weaknesses of Each Solution
Looking deeper into each software presents a clearer picture of their strengths and weaknesses:
Shop-Ware
Strengths:
- Intuitive interface, which reduces the learning curve for new users.
- Strong customer service support, enhancing user experience.
Weaknesses:
- May lack some advanced inventory management features compared to competitors.
Mitchell
Strengths:
- Comprehensive repair library providing in-depth service information.
- Excellent integration with diagnostic tools.
Weaknesses:
- Can be more expensive than other options, especially for small shops.
RepairShopr
Strengths:
- All-in-one solution that fulfills multiple business needs like CRM, invoicing, and reporting.
- Supports inventory tracking which is a major plus for parts-heavy businesses.
Weaknesses:
- User interface might feel cluttered and overwhelming for new users.
ProDemand
Strengths:
- Extensive diagnostic capabilities provide valuable data for repairs.
- Effective for shops focusing primarily on technical and diagnostic work.
Weaknesses:
- Does not have a dedicated financial management module, which may limit its usability for some shops.
A thorough understanding of each option's strengths and weaknesses is key to identifying the software that meets your unique operational demands.
In summary, the comparative analysis of available software solutions offers a framework for evaluating how well each platform can serve the specific needs of a diesel mechanic shop. By assessing these tools, shop owners can make informed decisions that not only enhance operational efficiency but also improve overall customer satisfaction.
The Future of Diesel Mechanic Shop Software
The future of diesel mechanic shop software is an essential aspect of the overall evolution of the automotive repair industry. As technology advances, the software in use can dramatically affect operational effectiveness in shops. Understanding the potential developments can assist shop owners in making strategic decisions to stay competitive.
Emerging Technologies
Emerging technologies are a significant factor influencing the future of diesel mechanic shop software. Innovations such as artificial intelligence (AI) and machine learning (ML) can enhance diagnostic tools. These technologies can analyze data from vehicles and suggest potential issues before they become severe. As a result, mechanics can provide better service and potentially increase customer retention.
In addition, mobile applications are becoming more prevalent. These apps streamline communication between customers and mechanics. They allow for easy scheduling of repairs, and updates on vehicle status can be sent directly to the customer's phone. This feature enhances customer experience.
Another key technology is Internet of Things (IoT) integration. IoT devices can monitor vehicle health in real-time. Using these devices can help mechanics anticipate issues and inform customers about necessary maintenance before it is critical. Accordingly, this technology supports preventive care, leading to customer satisfaction.
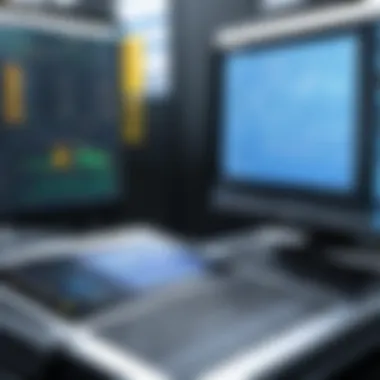
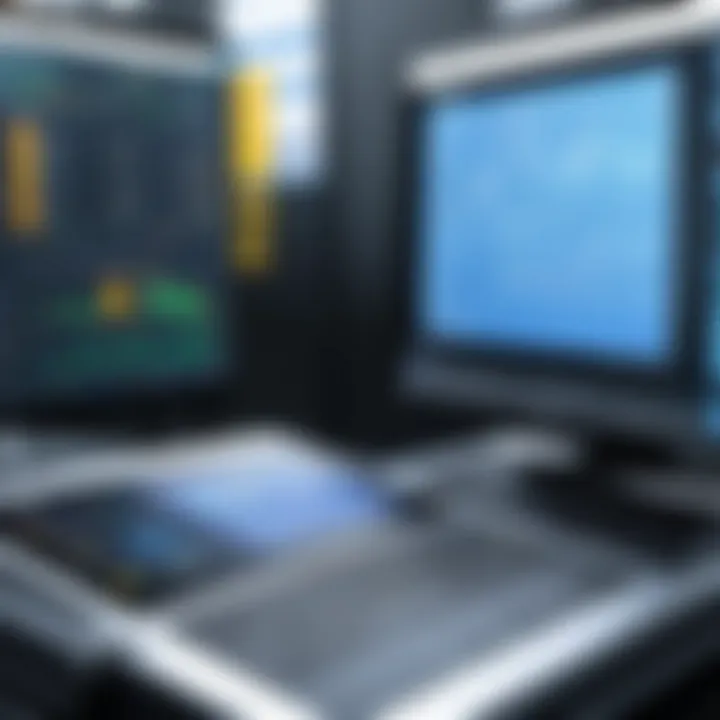
Predicted Market Growth
Market growth predictions for diesel mechanic shop software indicate a trend towards increased adoption by businesses. As mechanics increasingly recognize the advantages of software solutions, more shops will transition to digital systems. Several factors contribute to this growth.
The rising complexity of diesel engines requires effective data management solutions. Also, increasing customer expectations for transparency and quick service put pressure on workshops to optimize their operations. Software that can provide an integrated approach is likely to see a surge in demand.
Finally, reports suggest that the global market for automotive repair software may reach a substantial value by the end of this decade. Industry analysts predict high growth rates as more companies realize the efficiency and cost-saving benefits of modern software solutions. This projection emphasizes the necessity for shop owners to involve themselves with the ongoing advancements within this industry.
Security Considerations in Software Use
The implementation of software in diesel mechanic shops brings significant efficiencies. However, the importance of security considerations cannot be overlooked. Modern software solutions often handle sensitive data including customer information, financial records, and operational details. Addressing security concerns is paramount, as vulnerabilities can lead to data breaches, loss of customer trust, and in worst cases, legal consequences.
Investing in security-centric software design promotes integrity. Ensuring that the software you choose has robust security measures not only protects your business but also strengthens customer confidence. Additionally, regular software updates and security patches can prevent exploitation of known vulnerabilities. By proactively addressing security issues, diesel mechanic shops can maintain operational continuity and avoid potential reputational harm.
Data Protection Practices
Effective data protection practices are fundamental to safeguarding the information managed by diesel mechanic shop software. First and foremost, data encryption is critical. This process encodes data, rendering it unreadable to unauthorized users. Utilizing encryption ensures that even in the event of a data breach, the information remains protected.
Moreover, access controls should be implemented to restrict data access to authorized personnel only. This can include user authentication methods like multi-factor authentication. Training employees on data handling procedures also plays a role in minimizing accidental breaches. An informed workforce can identify potential threats and respond appropriately, further fortifying your data security.
Consider these best practices for data protection:
- Implement regular backups to prevent data loss.
- Utilize firewalls and antivirus software to defend against external threats.
- Conduct security audits to assess vulnerabilities and improve systems.
"Data is often referred to as the new oil, but it is only valuable if properly protected and utilized."
Regulatory Compliance
Regulatory compliance is another crucial aspect of using diesel mechanic shop software. Various regulatory standards govern how data must be handled, particularly sensitive customer information. Failing to comply can result in hefty fines and legal issues. Understanding the regulatory landscape is essential for any mechanical shop utilizing software solutions.
For instance, the General Data Protection Regulation (GDPR) encourages businesses to implement stringent controls over personal data. Non-compliance can lead to significant financial consequences. On the other hand, being compliant can enhance your shopโs credibility and reinforce customer trust.
Staying informed about relevant regulations and ensuring your software meets these standards will protect your business in the long run. Choosing vendors that prioritize compliance can make management easier. It is wise to regularly review your practices against existing regulations to ensure your shop remains compliant as laws evolve.
Integrating Software with Existing Processes
Integrating software with existing processes is a critical step for diesel mechanic shops. Successfully merging new technological solutions with traditional operations can significantly enhance productivity and efficiency. When shop owners adopt a new software system, it often replaces manual tasks and outdated procedures. Therefore, understanding how to achieve a seamless integration is paramount.
Transition Strategies
To ensure that the new software aligns with current operational workflows, several transition strategies can be employed. First, it is essential to conduct a thorough assessment of existing processes. This evaluation helps to identify any gaps or redundancies. Based on this analysis, a detailed plan can be developed outlining how each aspect of the new software will interact with current practices. Some key strategies include:
- Pilot Programs: Implementing the software in a selected area of the shop before a full rollout allows for adjustment based on real user feedback.
- User Training: Comprehensive training sessions for employees helps them understand the new system better. Knowledgeable employees are less resistant to change and can identify issues early.
- Incremental Integration: Instead of switching all systems at once, gradually introduce the software components. This method minimizes disruptions.
Challenges and Solutions
Despite careful planning, challenges in integrating new software may arise. Recognizing these potential obstacles can help in formulating effective solutions. Some common challenges include:
- Resistance to Change: Employees may prefer familiar processes, leading to pushback against the new system.
Solution: Open communication about the software's benefits along with involving staff in the transition can mitigate this resistance. - Data Migration Issues: Transferring data from older systems can result in loss or inaccuracies.
Solution: Use of robust data migration tools and pre-checks on data accuracy can reduce these risks. - Compatibility with Existing Tools: New software might not integrate well with other tools in use.
Solution: Research on software compatibility and looking for solutions with proven integration features is necessary.
"Integration of software is not just about technology; it's about people embracing change."
Training and Support for Software Users
The importance of proper training and support cannot be overstated when it comes to implementing diesel mechanic shop software. Training equips users with the skills needed to effectively operate the software, which can lead to maximizing its benefits. Users who are well trained can perform various functions such as managing inventory more efficiently, tracking work orders, and generating precise invoices. Inadequate training may result in the underutilization of features, causing potential setbacks and errors in service delivery.
Moreover, ongoing support enhances user experience. Software systems can be complex, and issues are likely to arise post-implementation. Access to reliable support can make a significant difference in how smoothly operations run. Both training and support foster confidence among staff, create an environment conducive to learning, and help in addressing specific issues that may not have been covered during initial training sessions. Thus, investing in these areas contributes significantly to overall business efficiency and customer satisfaction.
Best Practices for User Training
Effective user training is critical for the successful adoption of diesel mechanic shop software. Here are some best practices to consider:
- Tailored Training Sessions: Every shop has unique processes. Customized training ensures that users learn how to use software features relevant to their specific work environment.
- Hands-On Learning: Practical exercises during training allow users to interact with the software. This hands-on approach enhances retention of skills and knowledge.
- Use Training Materials: Providing manuals, videos, and guides can supplement training. Users often benefit from reviewing these resources at their own pace.
- Interactive Support: Encourage questions during training. Creating a comfortable environment where users can ask queries makes the training more effective.
- Feedback Mechanism: Implementing a feedback loop helps understand the trainingโs effectiveness. Feedback could lead to necessary adjustments and improve future training sessions.
Ongoing Support Options
Ongoing support must be an integral element of any software strategy. Effective support options contribute to user satisfaction and retention. Several approaches stand out:
- Help Desk Support: A dedicated team available for inquiries ensures users can quickly resolve issues as they arise.
- Regular Updates: Keeping the software updated with the latest fixes and enhancements can prevent issues and improve functionality.
- User Forums: Setting up forums or discussion boards allows users to help each other and share best practices. This community aspect can enhance user engagement and knowledge sharing.
- Training Refreshers: Periodic training sessions re-engage users with the software. This could be crucial when new features are introduced.
- Performance Monitoring: Regularly assessing how users interact with the software can provide insights into areas needing additional support or training.
Investing in training and support is vital to extracting maximum value from diesel mechanic shop software. Without these elements, a business may struggle to achieve the operational efficiencies intended.
Costs Associated With Diesel Mechanic Shop Software
Understanding the costs associated with diesel mechanic shop software is essential for shop owners who aim to balance investment with operational benefits. The decision to adopt such systems can have significant financial implications. Therefore, an analysis of both initial investment and long-term costs is crucial.
Initial Investment
When considering diesel mechanic shop software, the initial investment reflects the upfront costs incurred in acquiring the software. This may involve several components, such as:
- Software Purchase Price: The licensing fees for the software itself can vary significantly based on features and functions. Premium software may deliver advanced capabilities but at a higher price.
- Hardware Requirements: Depending on the software, there might be a need for new computers or servers to run the system efficiently.
- Installation Costs: Additional expenses may arise from configuring the software within existing systems or from third-party installation services.
- Training Expenses: Implementing new software often requires user training to ensure staff can utilize it effectively. This is not only a cost but also an investment in time.
Evaluating these factors helps in determining if the investment aligns with the anticipated returns. A clear understanding of these initial expenditures allows for better budgeting and planning.
Long-term Financial Implications
The long-term financial implications can be as significant as the initial costs. While the upfront investment might seem daunting, the overall operational efficiencies gained can result in considerable savings over time. Some key considerations include:
- Maintenance and Support Costs: Over time, software may require updates or ongoing technical support, which can entail additional costs. It's vital to account for these in the budgeting process.
- Increased Efficiency and Productivity: By streamlining operations, the software can lead to reduced labor costs and improved productivity. This, in turn, helps in justifying the initial investment over time.
- Return on Investment (ROI): Long-term benefits can be quantified, and itโs important to assess how quickly one can expect to see a return on the investment. Businesses should create projections on how the software will enhance service delivery and customer satisfaction.
- Scalability Costs: As the business grows, the software may need upgrades. Factor in costs that arise from scaling the software to meet higher demand.
"Understanding these costs allows shop owners to make informed decisions about software investments which ultimately drive their business success."
Ending
In this article, the importance of diesel mechanic shop software has been underlined through various discussions surrounding its features, benefits, and the necessary elements for selection. Diesel mechanic shops experience diverse operational challenges. Thus, having tailored software can significantly streamline these processes. The conclusion encapsulates the key insights drawn from the previous sections and establishes a foundation for implementing such systems effectively.
Summarizing Key Insights
The analysis reveals that durability, efficiency, and user-friendliness are essential in selecting diesel mechanic shop software. Here are some crucial insights:
- Enhanced Efficiency: Properly integrated software reduces manual work and saves time.
- Accuracy in Record Keeping: Automated systems improve data accuracy and minimize human error.
- Customer Relations: Robust CRM features foster better communication with clients, enhancing customer satisfaction.
Overall, shops that embrace these software solutions can expect improvements in operations and overall profitability.
Final Recommendations
While selecting diesel mechanic shop software, consider the following recommendations:
- Assess Specific Needs: Each shop is unique; understanding particular operational challenges is vital.
- Prioritize User Support: Ensure that the chosen software offers comprehensive training and ongoing support, as adaptability is key for your team.
- Financial Considerations: Weigh the initial and long-term costs against the potential returns of investing in this software.
- Explore Integration Options: Determine how well the software can integrate with existing systems, which is critical for smooth transitions.
Implementing the right diesel mechanic software is not merely an upgrade; it is a strategy for enhanced operational excellence. By focusing on these specific aspects and insights, mechanics and shop owners can make informed decisions that benefit their business in the long term.
"The right software solution can empower diesel mechanic shops to thrive in an increasingly competitive landscape."