Kaizen in Fleet Management: Boosting Efficiency
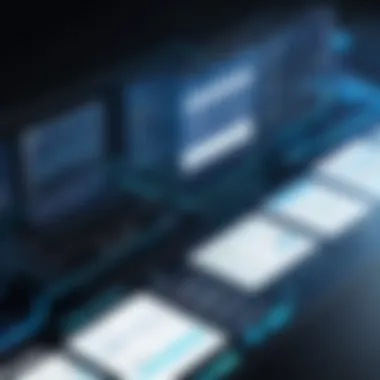
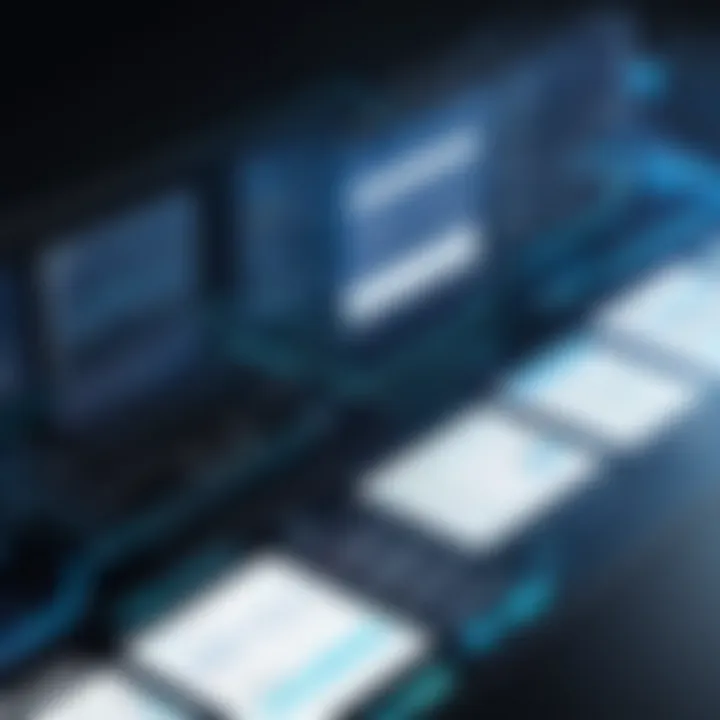
Intro
In the fast-paced world of fleet management, staying ahead requires more than just keeping the wheels turning. It demands a keen eye on efficiency, cost management, and continuous improvement. Here, the philosophy of Kaizen, which essentially means "change for the better," becomes a cornerstone for success. By weaving Kaizen principles into the fabric of fleet operations, organizations can identify opportunities for incremental improvements that lead to significant operational benefits.
This approach promotes a culture where every team member, from drivers to management, feels empowered to suggest and implement small changes that can lead to big results. In fleet management, where every mile driven and gallon of fuel used impacts the bottom line, applying Kaizen strategies can enhance productivity and employee satisfaction alike.
Next, let's delve into the essential areas that facilitate the adoption of Kaizen in fleet management, starting with a comprehensive Software Needs Assessment.
Foreword to Kaizen and Fleet Management
In today's fast-paced commercial environment, where every dime counts, the capability to fine-tune operations offers companies a distinct edge. This is where the combination of Kaizen and fleet management comes into play. Kaizen, a Japanese term meaning "continuous improvement," stresses the need for incremental advancements rather than waiting for a singular overhaul. Combining this philosophy with fleet management can turn the gears of efficiency, directly influencing both operational cost and overall service quality.
Defining Kaizen
At its core, Kaizen is about small, consistent changes that accumulate over time to generate significant improvements. Originally rooted in Japan's industrial age, it has transcended its origins to become a universal method for organizations aiming for operational excellence. In practice, it's not merely a management tool but a way of thinking that invites employees at all levels to partake in the process. This implies that every team member, from the driver to the fleet manager, has a role in suggesting and implementing enhancements. It's no surprise that companies that adopt this mindset often find themselves ahead of the competition.
Understanding Fleet Management
Fleet management refers to the administration of commercial vehicles, including cars, trucks, and vans. Efficient fleet management involves keeping tabs on various elements such as vehicle maintenance, fuel management, routing, and regulations. It also encompasses the orchestration of logistics to ensure goods reach their destination timely and safely. A well-managed fleet not only translates to cost savings but also enhances customer satisfaction and boosts employee morale when deliveries are made smoothly. When one considers the shear scale of fleet operations, it becomes clear that small operational tweaks can result in major savings.
The Intersection of Kaizen and Fleet Management
Bringing Kaizen into fleet management creates a fertile ground for continuous enhancement. By analyzing current processes within fleet management, businesses can pinpoint inefficiencies and find avenues to improve. Picture this: a transportation company unhappy with its fuel costs implements a series of minor changes—modifying driver routes, improving vehicle maintenance schedules, or adopting eco-driving tips. Over time, these small actions can lead to dramatic reductions in fuel use and associated costs. Integrating Kaizen fosters a culture of innovation and adaptation in an industry that depends on effective and efficient processes for survival.
"The journey of a thousand miles begins with one step."
— Lao Tzu
By adopting a continuous improvement mindset integrated with fleet management practices, organizations not only enhance their operational efficiency but also cultivate a more engaged workforce, ultimately driving growth and reducing waste.
Principles of Kaizen in Fleet Management
The implementation of Kaizen principles in fleet management carries profound implications for organizations striving for efficiency and cost reduction. By embedding an ethos of continuous improvement, companies can not only streamline their operations but also cultivate a culture where every employee feels their contributions matter. Success in fleet management hinges on a clear understanding of these principles, which can pivot a business towards sustainable growth and operational excellence.
Continuous Improvement Philosophy
The heart of Kaizen lies in its philosophy of continuous improvement. This mantra insists that no matter how well a system is functioning, there’s always room for improvement. Within the framework of fleet management, this means regularly assessing and refining processes—be it vehicle maintenance schedules, routing strategies, or fuel consumption monitoring.
Adopting this mindset encourages teams to seek better methods, often in small but impactful ways. For example, instead of overhauling an entire fleet logistics strategy at once, managers can experiment with adjustments in load distribution or fuel types. These incremental changes can yield significant cumulative benefits over time. As maintenance routines are tweaked or route effectiveness is regularly evaluated, organizations can uncover hidden inefficiencies that might otherwise go unnoticed. These tweaks often lead to enhanced productivity and, ultimately, cost savings.
"Small changes add up to big results."
Employee Involvement and Empowerment
For Kaizen to gain a foothold in fleet management, it’s critical to involve employees at all levels. When team members are active participants in the improvement process, they take ownership of their roles and contribute to the overall success of the organization. Empowering employees—whether drivers, maintenance staff, or logistics coordinators—means granting them the authority to suggest changes and identify problems in their daily operations.
In practice, this could involve establishing regular team meetings where employees can share insights about routing inefficiencies or equipment issues. By giving a voice to those who are hands-on, companies not only boost morale but also frequently discover practical solutions that management may overlook. Additionally, recognition programs for suggesting improvements foster a positive atmosphere that encourages innovation and collaboration.
Focus on Quality and Efficiency
Kaizen's emphasis on quality suggests that success in fleet management isn’t solely about maintaining productivity metrics. It's equally about ensuring high-quality services and sustainability practices. Quality can be manifested in several areas, like customer service, vehicle reliability, and safety habits among drivers.
Efficiency, on the other hand, relates to optimizing resources—managing fuel consumption, reducing idle times, and maximizing vehicle usage. An integrated approach that incorporates both quality and efficiency will yield a well-rounded fleet strategy. For instance, implementing telematics in vehicles can provide real-time data on driver behavior and vehicle performance, allowing for immediate corrective measures.
Consequently, organizations embrace technology not only to track performance but also to enforce compliance with safety standards. By refining both quality and efficiency through the lens of Kaizen, fleet management can lead to better outcomes for the business and its customers, thus fostering long-term loyalty and trust.
Implementing Kaizen in Fleet Management Operations
When it comes to fleet management, implementing Kaizen isn't just another buzzword; it's a game changer. It's about more than just cutting costs or trimming fat—it's about creating a culture where small, incremental changes lead to significant overall improvements. Kaizen, at its core, fosters an environment where everyone, from the management down to the ground level, is encouraged to contribute ideas for betterment. This collaborative approach taps into the collective intelligence of the team, optimizing fleet operations effectively.
By embedding Kaizen principles into fleet operations, companies can streamline workflows, enhance safety, and ultimately deliver better services to customers. But where does one start? This discussion covers vital steps in implementing Kaizen specific to fleet management—highlighting the importance of establishing performance checkpoints, pinpointing improvement areas, framing action plans, and supporting staff development.
Establishing a Baseline for Performance
Setting the stage for any improvement initiative begins with understanding the current state of your fleet operations. Establishing a baseline for performance is crucial. This means gathering data on existing operational metrics like vehicle utilization, fuel consumption, maintenance costs, and driver behavior. Essentially, it’s the starting line from which all improvements will be measured.
Tools like telematics systems can provide insight into vehicle performance and driver habits, while maintenance logs detail costs and downtime. By collecting this information, fleet managers can identify benchmarks and set realistic goals. It’s a bit like wanting to run a marathon; you can't just lace up your shoes and expect to win unless you've tracked your training progress and know where to improve.
Identifying Areas for Improvement
Once you’ve established a reliable baseline, the next task is to identify areas that need a little TLC. This step can sometimes feel intimidating, as it requires an honest assessment of operations. Engaging with your team through regular feedback loops can help shed light on inefficiencies that might fly under the radar.
Conduct brainstorming sessions or use suggestion boxes to gather input. Common areas of improvement could include:
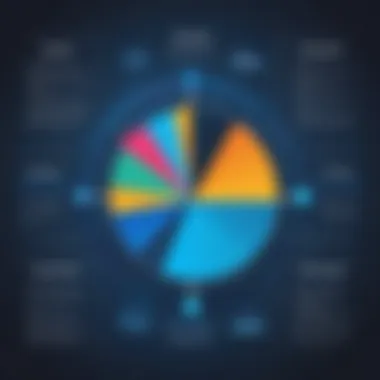
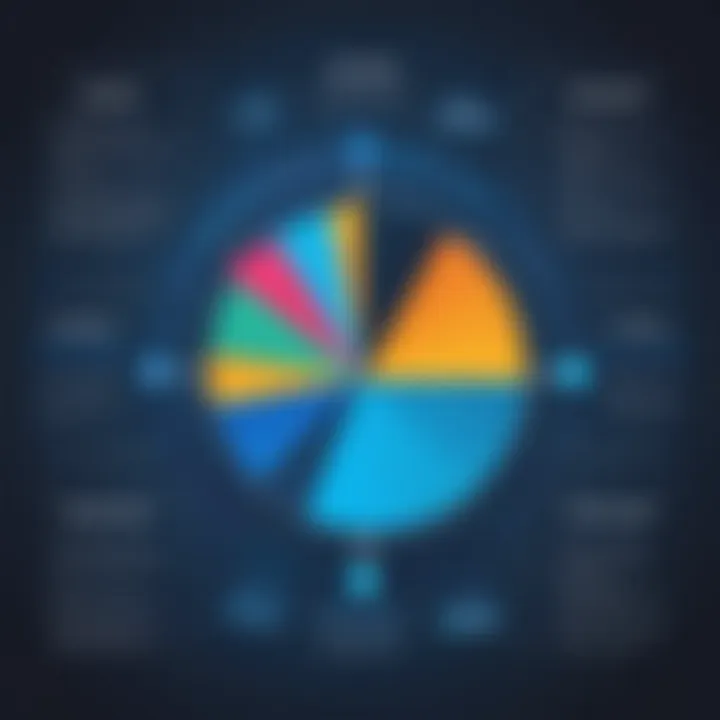
- Routing Optimization: Are drivers taking the most efficient paths?
- Fuel Efficiency: What are the driving habits contributing to excessive fuel consumption?
- Maintenance Procedures: Is preventative maintenance being performed on schedule to avoid breakdowns?
Being open to recognizing both the strengths and weaknesses in operations helps create a balanced view of where changes can yield the best returns.
Developing Action Plans
Once the key improvement areas are identified, it’s time to draft action plans. This part involves mapping out specific strategies to tackle each issue—with clear objectives and timelines. Each plan should include:
- Goals: What does success look like?
- Responsibilities: Who’s accountable for each action?
- Resources Needed: What tools or training may be necessary to achieve these goals?
- Milestones: How will progress be monitored?
For instance, if routing is identified as a weak link, setting a plan to integrate routing software could be a critical step. Action plans should be flexible, allowing room for adjustments as necessary to accommodate new insights or challenges that may arise along the way.
Training and Development of Staff
Training staff is where the rubber meets the road, literally. To carry out the Kaizen philosophy effectively, the workforce needs to be equipped with the right skills and knowledge. This isn’t just about formal training sessions. Ongoing development and support are crucial to nurturing a Kaizen culture.
Consider the following:
- Workshops: Regular workshops can keep everyone on the same page regarding best practices.
- Mentoring: Pairing experienced employees with newer team members can facilitate skill transfer and problem solving.
- Feedback Mechanisms: Encouraging self-reflection and team assessments fosters a culture of continuous learning.
Ultimately, your fleet's success hinges on how well-equipped your drivers and staff are. Investing in them isn’t just a cost; it’s a strategic move towards fostering a proactive work environment that embraces change.
Implementing Kaizen in fleet management operations, therefore, is a process that requires the commitment not just to fix inefficiencies but to enhance the workplace culture as well. By laying a strong foundation, identifying areas ripe for improvement, drafting actionable plans, and investing in staff training, companies can harness the full potential of Kaizen. This transforms not only the fleet's efficiency but also contributes to an overall increase in satisfaction, both for employees and end-users.
Measuring the Impact of Kaizen on Fleet Operations
Measuring the impact of Kaizen on fleet operations is crucial for understanding how continuous improvement strategies transform productivity. This evaluation goes hand-in-hand with identifying both quantitative and qualitative dimensions of efficiency. Organizations can’t just implement new processes and hope for the best. They need solid metrics that show how those changes ripple through daily operations and lead to tangible benefits. Moreover, establishing measurable outcomes helps with employee engagement, as teams see the fruits of their labor and are more likely to participate actively in future initiatives.
Establishing Key Performance Indicators (KPIs)
Key Performance Indicators are essential tools in this journey. By setting specific KPIs, fleet managers can gauge performance in various aspects. Typical KPIs may include:
- Fuel efficiency: Measures the average gallons used per mile, serving as a direct indicator of operational efficiency.
- Vehicle utilization rates: Highlights the percentage of time vehicles are actively used versus being idle.
- Maintenance costs per vehicle: Registering the expense incurred for repairs and upkeep, aiding in understanding where resources are best allocated.
- On-time deliveries: A key metric reflecting the timeliness and reliability of fleet services.
When crafting KPIs, it's crucial to ensure they align with overall business goals. For instance, if a company aims to cut maintenance costs, then that KPI should be prioritized and closely monitored. Specific, measurable, achievable, relevant, and time-bound criteria should be used when developing these indicators.
Data Collection and Analysis Techniques
Once KPIs are established, the next step involves data collection. In fleet management, data can be gathered from numerous sources including:
- Telematics systems: These tools track vehicle performance and driver behavior, feeding valuable data into the analysis process.
- Fleet management software: Programs designed for tracking expenses, route optimization, and vehicle conditions can offer dynamic insights.
- Surveys and feedback forms: Gathering input from drivers and fleet staff can uncover areas where Kaizen could be applied effectively.
After data is collected, it requires thorough analysis. Techniques such as root cause analysis and trend analysis can help pinpoint inefficiencies. By regularly reviewing this information, fleets can identify the improvements that yield the best results, tailoring their strategies to optimize performance continually.
Continuous Feedback Loops
A critical part of implementing Kaizen principles is creating continuous feedback loops. This system enables real-time adjustments and fosters an environment of ongoing improvement. Feedback loops can take various forms, including:
- Monthly performance reviews: Bringing together stakeholders to discuss KPI outcomes ensures that everyone is on the same page.
- Regular team meetings: These forums allow fleet members to share successes and challenges, promoting a culture of inclusion.
- Dashboards: Visual tools to display KPIs and data trends in an easily digestible format, helping even non-tech-savvy members understand performance metrics.
Creating a culture of feedback means acknowledging both successes and setbacks. This encourages teams to participate actively in improvement processes. Employing these feedback loops not only keeps all members informed, but also strengthens employee engagement and contributes to the overall success of Kaizen initiatives.
By understanding and measuring the impact of Kaizen, fleets can not only increase efficiency and reduce costs but also foster a culture where continuous improvement becomes the norm rather than an exception.
Adopting these strategies ensures that Kaizen principles effectively take root in fleet operations, turning incremental changes into significant performance gains.
Challenges in Applying Kaizen to Fleet Management
In an ever-evolving landscape of fleet management, the principles of Kaizen present a roadmap for improvement. Yet, diving into this journey isn't without its bumps along the way. Recognizing the challenges associated with implementing Kaizen provides a clearer picture of how organizations can navigate these hurdles effectively. The path to systematic enhancement often requires a delicate balance between ambition and reality, especially in a field that demands both operational efficiency and adaptability.
Resistance to Change
One of the most significant roadblocks encountered is resistance to change. It’s a common sentiment for employees to feel uneasy when faced with new processes. Change can stir the waters and prompt discomfort. In the world of fleet management, where routines are often ingrained, the methodology of Kaizen can feel alien.
Understanding that this resistance isn’t just a barrier, but also an opportunity for growth is essential. It’s crucial for management to engage staff early in discussions surrounding Kaizen initiatives. By fostering an environment where feedback is welcomed, managers can alleviate fears and cultivate a culture that views change as a stepping stone rather than a stumbling block.
"Most of the change is mental. We need to shift our mindset first before shifting our operations." — A Fleet Manager reflecting on his experience.
Building an emotional connection to the goals of the Kaizen approach can transform skepticism into enthusiasm. Through training sessions, demonstrations, and involving team members in decision-making, it's possible to carve a path through resistance. As a step further, recognition of early adopters can motivate the team to embrace change collectively.
Resource Limitations
Another challenge faced in applying Kaizen principles is resource limitations. Be it time, money, or human capital, constraints can make the continuous improvement journey feel daunting. Every fleet operates under the pressure of tight budgets and schedules, making it challenging to allocate resources for new initiatives.
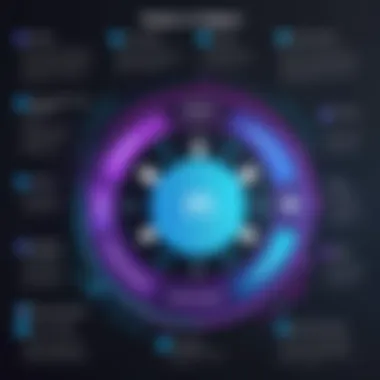
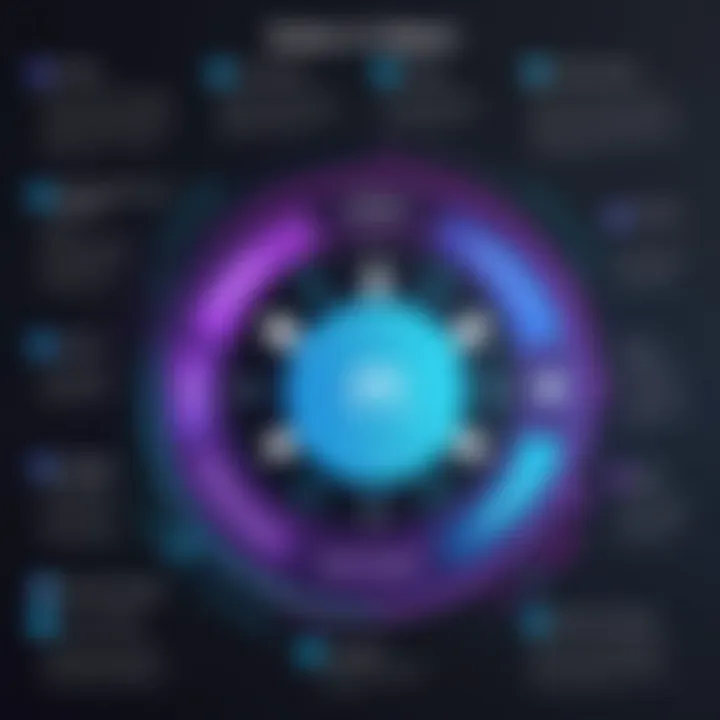
To tackle these limitations successfully, it's vital to prioritize feature efforts that deliver the most substantial impact. For instance, focusing on small, manageable improvements can provide immediate benefits without overwhelming lean resources. Incorporating Kaizen doesn’t always mean sweeping changes, but rather optimizing what’s already in place.
Consider implementing cost-effective software solutions for tracking performance. These tools can yield insights on areas requiring enhancement and streamline operations without needing hefty investments. Moreover, leveraging existing staff to spearhead small projects encourages a sense of ownership and not just added workload, making the task less daunting.
Maintaining Employee Engagement
Employee engagement plays a crucial role in the success of Kaizen initiatives, yet keeping staff motivated poses its own challenges. When day-to-day duties overshadow long-term goals, some may lose sight of the benefits continuous improvement can provide.
So, how do you keep the flame of engagement alive? One way is to celebrate small wins. Highlighting achievements, no matter how minor, creates momentum and reinforces the value placed on employee contributions. Not only does this foster a sense of accomplishment, but it also reminds the team of their part in the larger mission of the organization.
In addition, regular check-ins can help maintain enthusiasm. Simple one-on-one discussions about progress and barriers allow for open dialogue. This transparency encourages workers to voice concerns and share ideas while reinforcing their role in Kaizen practices.
Prioritizing recognition isn’t just about the individuals, but also the team. Whether through informal gatherings or formal award ceremonies, recognizing collective effort further cements an engaged culture where Kaizen can thrive.
In summation, while challenges abound in applying Kaizen principles to fleet management, addressing these obstacles with targeted strategies can pave the way for sustained growth and improvement. Understanding resistance, managing resources effectively, and cultivating employee engagement are cornerstones that will fortify the implementation of Kaizen, ultimately enhancing overall efficiency in fleet operations.
Case Studies of Successful Kaizen Implementation
Understanding how theory translates into practice can be critical when it comes to Kaizen and its place in fleet management. Case studies exemplify how various companies have successfully integrated Kaizen principles into their operational strategies. By analyzing these real-world scenarios, businesses can glean insights, identify best practices, and understand the tangible benefits of continuous improvement. It's not just about the changes themselves, but the methodology behind these transformations that provides a roadmap for others aiming to enhance efficiency.
Company A: Optimizing Routing Efficiency
A notable case involves a logistics firm that faced rising fuel expenses and delays in delivery times. By employing Kaizen concepts, they initiated a project focused on optimizing routing efficiency. The team began with a thorough analysis of their existing routes, utilizing data-driven approaches and GPS tracking to pinpoint inefficiencies.
Several strategies were applied:
- Data Review: Routes were mapped out and scrutinized for frequent traffic bottlenecks or redundancies.
- Stakeholder Engagement: Input was gathered from drivers who knew the ins and outs of the roads. Their practical experiences highlighted areas that the management may have overlooked.
- Incremental Adjustments: Small changes were tested, such as altering delivery windows and consolidating shipments. The emphasis was on making one change at a time, followed by assessment.
The results were impressive. Within six months, the company recorded a 20% reduction in fuel consumption and improved delivery times by a notable margin. This initiative exemplified how Kaizen principles, when applied thoughtfully, can lead to significant enhancements in fleet operations and bottom-line savings.
Company B: Reducing Maintenance Costs
Another exemplary case is that of a medium-sized transportation company which struggled with exorbitant maintenance costs for its vehicle fleet. Embracing a Kaizen approach allowed them to tackle the problem systematically. The initial phase involved collecting data on maintenance schedules and costs over time to establish a clear picture of the existing state.
Key actions taken included:
- Preventive Maintenance Program: Traditional reactive maintenance was replaced with a preventive strategy based on data insights. This shift reduced breakdowns and extended vehicle life.
- Staff Training: Technicians were educated on best practices in vehicle upkeep, ensuring all team members understood the Kaizen methodology.
- Continuous Monitoring: Implementation of maintenance monitoring software enabled ongoing assessment of vehicle performance, leading to timely interventions.
This transformation culminated in a two-year period wherein the company slashed maintenance costs by 30%. It illustrated that aligning staff capabilities with Kaisen principles can yield substantial financial benefits and operational stability.
Company C: Enhancing Driver Training Programs
Lastly, a leading delivery service sought to improve safety and efficiency through enhancements in driver training programs. They recognized that the performance of their drivers was pivotal to company objectives. Applying Kaizen meant refining these training programs with an eye towards incremental improvement.
The strategies employed were as follows:
- Feedback Loops: Drivers were encouraged to provide input on the training materials, ensuring that the content was relevant and engaging.
- On-the-Road Assessments: Regular evaluations of driving habits were initiated, allowing real-time feedback and coaching.
- Flexible Learning Modules: The training program evolved into modular content that could be tailored to individual driver needs, ensuring personalized learning paths.
As a result, the company saw a significant drop in accident rates and improved on-time delivery metrics. The continuous improvement approach demonstrated how adapting training processes through Kaizen can not only enhance driver performance but also reinforce a positive safety culture across the organization.
"Case studies illuminate the path others can tread; they show what’s possible when Kaizen meets everyday operations."
These three cases reveal that embracing Kaizen in fleet management isn't about hitting a home run every time, but rather focusing on making a series of small, impactful changes that accumulate over time to drive significant enhancements.
Tools and Resources for Kaizen in Fleet Management
In the fast-paced world of fleet management, having the right tools and resources at hand can make all the difference. The integration of various resources enhances the implementation of Kaizen principles, allowing for continuous improvement across all levels of operations. It's no small feat, but with the right elements, organizations can foster an environment where efficiency thrives.
Software Solutions for Data Analysis
As we step into a data-driven era, software solutions play an indispensable role in analyzing fleet performance. Programs such as Tableau and Microsoft Power BI allow managers to visualize data effectively, helping them to draw meaningful insights. By leveraging these tools, organizations can identify trends, track key performance indicators, and ultimately make informed decisions that enhance fleet operations.
Some notable aspects to consider when selecting software for data analysis include:
- User-Friendliness: Select software that teams can easily navigate to mitigate training time.
- Integration Capabilities: Ensure the tool can integrate with existing fleet management systems.
- Real-Time Reporting: Opt for solutions that offer instant data updates, allowing for timely responses to issues.
Furthermore, data visualization simplifies the explanation of complex stats, making it easier for decision-makers to grasp performance metrics. As they say, “A picture's worth a thousand words.” In this case, a well-designed data dashboard is worth its weight in gold, enabling stakeholders to zero in on critical areas for improvement.
Best Practices for Documenting Procedures
Effective documentation underpins successful Kaizen implementation. Having standardized procedures not only promotes consistency but also serves as a baseline for measuring improvements. Documenting procedures involves more than merely writing down steps; it requires a meticulous approach to ensure clarity and accessibility.
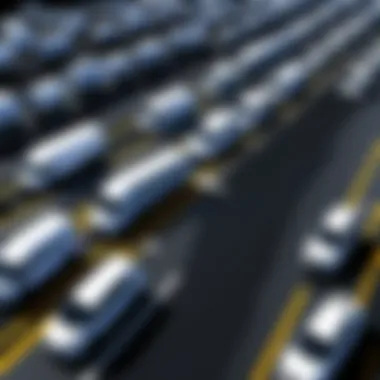
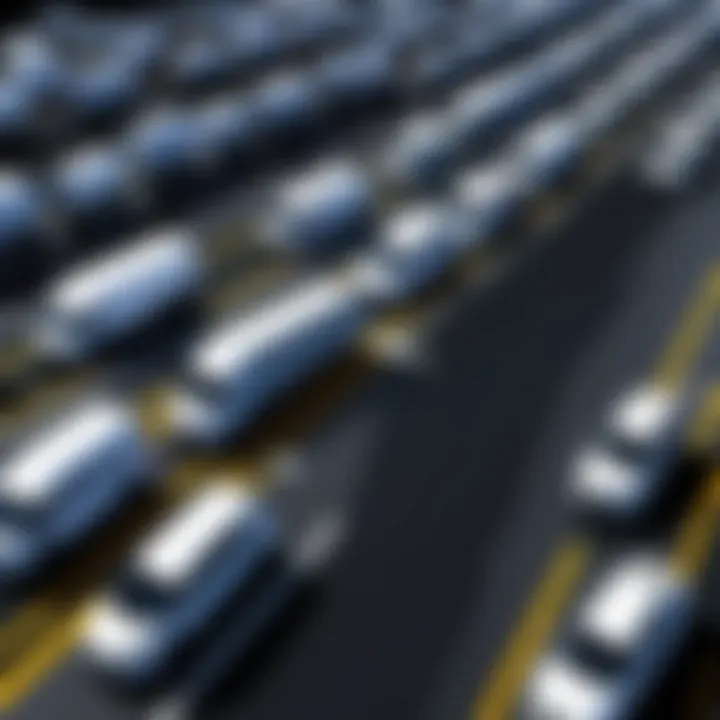
Here are effective ways to document procedures:
- Flowcharts and Diagrams: Visual aids can significantly enhance understanding. Using flowcharts to map out processes can provide clarity to employees who benefit from visual learning.
- Regular Updates: As processes evolve, so should documentation. Foster a culture of continual revisions to keep records relevant and accurate.
- Train Employees on Documentation: It's essential that employees understand the documentation process. Investing time in training ensures everyone knows their part in maintaining up-to-date records.
By establishing clear and thorough documentation, organizations can facilitate smoother training processes and alleviate the learning curve for new team members, ultimately enhancing employee engagement.
Online Communities and Forums
In today's interconnected world, online communities provide a wealth of collective knowledge. Platforms like Reddit and various Facebook groups offer spaces for fleet managers to share experiences, challenges, and solutions. Engaging actively in these forums can provide valuable insights and real-world examples that often don’t make it into traditional case studies.
Benefits of participating in online communities include:
- Networking Opportunities: Engaging with peers can lead to potentially beneficial partnerships and collaborations.
- Access to Expert Opinions: Many forums include seasoned professionals who can offer unique perspectives and tips.
- Resource Sharing: Members often share relevant articles, software tools, and frameworks that can provide fresh ideas for continuous improvement.
The essence of Kaizen is rooted in collaboration and shared learning. When fleet management professionals gather in these spaces, they contribute to an ever-expanding pool of knowledge that supports individual and organizational growth.
"The only source of knowledge is experience."
- Albert Einstein
By harnessing these tools and resources, the application of Kaizen principles in fleet management can transform operations significantly. Continuous improvement isn't just an ideal; it's an attainable reality with the right support mechanisms in place.
Future Trends in Kaizen and Fleet Management
Examining the upcoming trends in Kaizen's application within fleet management reveals that this philosophy is not only evolving but is also poised to radically reshape how organizations conduct their operations. Integrating advanced technology with the principles of continuous improvement allows businesses to harness efficiency like never before. This section will touch on transformative elements such as artificial intelligence, the emergence of autonomous vehicles, and a stronger focus on sustainability within the Kaizen framework.
Integration of Artificial Intelligence
Artificial intelligence (AI) is a game changer in fleet management. By analyzing vast amounts of data gathered from various sources—like GPS systems, telematics, and driver behavior—AI can provide insights that are far beyond the human capacity. Fleet managers can predict maintenance needs, optimize routes in real-time, and even evaluate driver performance.
AI's ability to learn from patterns is where the magic happens. For example, an AI-driven system can identify trends in vehicle performance and suggest specific action plans to enhance durability or fuel efficiency. Here are a few ways AI is revolutionizing fleet management through Kaizen:
- Data-Driven Decision Making: Continuous improvement is most effective when decisions are backed by solid data. With AI, fleet managers can rely on accurate forecasts and analytics.
- Predictive Maintenance: Rather than relying on scheduled checks, AI enables predictive maintenance that helps avoid costly repairs and downtime.
- Enhanced Safety Monitoring: AI tech can alert managers about unsafe driving patterns or malfunctions, allowing for timely interventions.
"By embedding AI into fleet management, we can not only enhance operational efficiency but also cultivate an environment of proactive problem-solving."
The Role of Autonomous Vehicles
The dawn of autonomous vehicles is just around the corner, and their role in fleet management cannot be understated. These vehicles promise to reshape traditional approaches to Kaizen. Imagine a fleet of self-driving trucks that can communicate with one another, optimizing fuel consumption and reducing wait times during deliveries.
Autonomous vehicles bring their own set of advantages:
- Reduced Labor Costs: With fewer drivers needed, companies can reallocate resources to other tasks.
- Increased Utilization Rates: Self-driving vehicles can operate continuously without the need for rest. This boosts overall productivity.
- Consistent Performance: Machines can provide more reliability in performance than human drivers, leading to fewer accidents and operational hiccups.
The challenge, of course, lies in the transition. Companies must consider how to integrate these vehicles smoothly with existing operations while ensuring compliance with regulations.
Sustainability and Kaizen Practices
Sustainability is not just a buzzword; it's becoming a pressing requirement for businesses worldwide. As the climate crisis continues to escalate, fleet management needs to adopt environmentally friendly practices. Integrating sustainability within Kaizen can lead to significant benefits both for the environment and cost management.
Here are some avenues for infusing sustainability into daily operations:
- Green Fleet Initiatives: Investing in electric or hybrid vehicles can drastically reduce carbon footprints.
- Fuel Efficiency Measures: Continuous monitoring of fuel consumption patterns can reveal opportunities for improvement.
- Recycling Practices: Efficiently managing waste by recycling parts and materials reduces operational costs and environmental impact.
To sum up, embedding sustainability into the Kaizen philosophy means that organizations can address both operational efficiency and the ethical imperative to protect our planet. It's about smarter practices today for a healthier tomorrow.
Ending
In the realm of fleet management, the integration of Kaizen principles can significantly shift operational dynamics. As we reflect on the insights detailed throughout this discourse, it becomes evident that continuous improvement is not just a methodology; it's a mindset that can lead to transformative changes.
One of the pivotal elements highlighted is the importance of establishing a culture where every employee is encouraged to contribute ideas for improvement. Whether it's a driver suggesting a new route or a maintenance technician identifying recurring issues, tapping into the collective intelligence of the workforce fosters ownership and engagement. This democratization of improvement initiatives builds a strong foundation for shared success.
Furthermore, the benefits of clear metrics and performance indicators cannot be overstated. By defining and regularly tracking Key Performance Indicators (KPIs), organizations position themselves to react swiftly to deviations in performance, ensuring that operational efficiency remains a top priority. In light of these insights, implementing Kaizen practices also brings along considerations like the necessity for consistent training and development, which enhances the skills of the staff while keeping them motivated and aligned with the company's goals.
Efforts towards continuous improvement foster an environment where innovation thrives. As the case studies illustrated, companies that adopted Kaizen not only saw cost reductions but also enhanced employee satisfaction and customer service levels, creating a win-win scenario for everyone involved. The ripple effect reaches beyond immediate financial benefits; it embeds a philosophy of excellence that can redefine entire fleets.
"Continuous improvement is better than delayed perfection."
Recap of Key Insights
- The interaction between Kaizen principles and fleet management breeds a culture of constant improvement.
- Employee involvement is crucial; every team member has a role to play in suggesting improvements.
- Establishing and monitoring KPIs keeps teams focused and allows for timely adjustments.
- Continuous training is essential to maintain engagement and enhance workforce skills.
- Successful Kaizen implementation leads to cost reductions and greater customer satisfaction.
Future Outlook for Kaizen in Fleet Management
Looking forward, the application of Kaizen in fleet management is poised to evolve significantly. As technology continues to advance, tools for data analysis will become more sophisticated, enabling more precise monitoring and swift implementation of improvement initiatives.
Moreover, the integration of artificial intelligence has the potential to streamline operations even further. Predictive analytics can forecast maintenance needs, optimize routing more efficiently, and enhance driver performance through tailored training regimens based on real-time data. The concept of autonomous vehicles also ties into this future perspective, suggesting a landscape where human oversight and machine efficiency work hand in hand to foster operational excellence.
Sustainability trends are also shaping the conversation around fleet management. Companies are increasingly feeling the pressure to reduce their carbon footprints. Implementing Kaizen practices that emphasize efficiency and responsible resource use can directly contribute to meeting those sustainability goals.
In essence, the future of Kaizen within fleet management is bright, filled with opportunities for innovative approaches that promise to drive efficiency, cost savings, and sustainability in equal measure. As organizations adapt and evolve, the principles of continuous improvement will undoubtedly steer them toward a more flexible and resilient operational framework.